What is P3 3D printing?
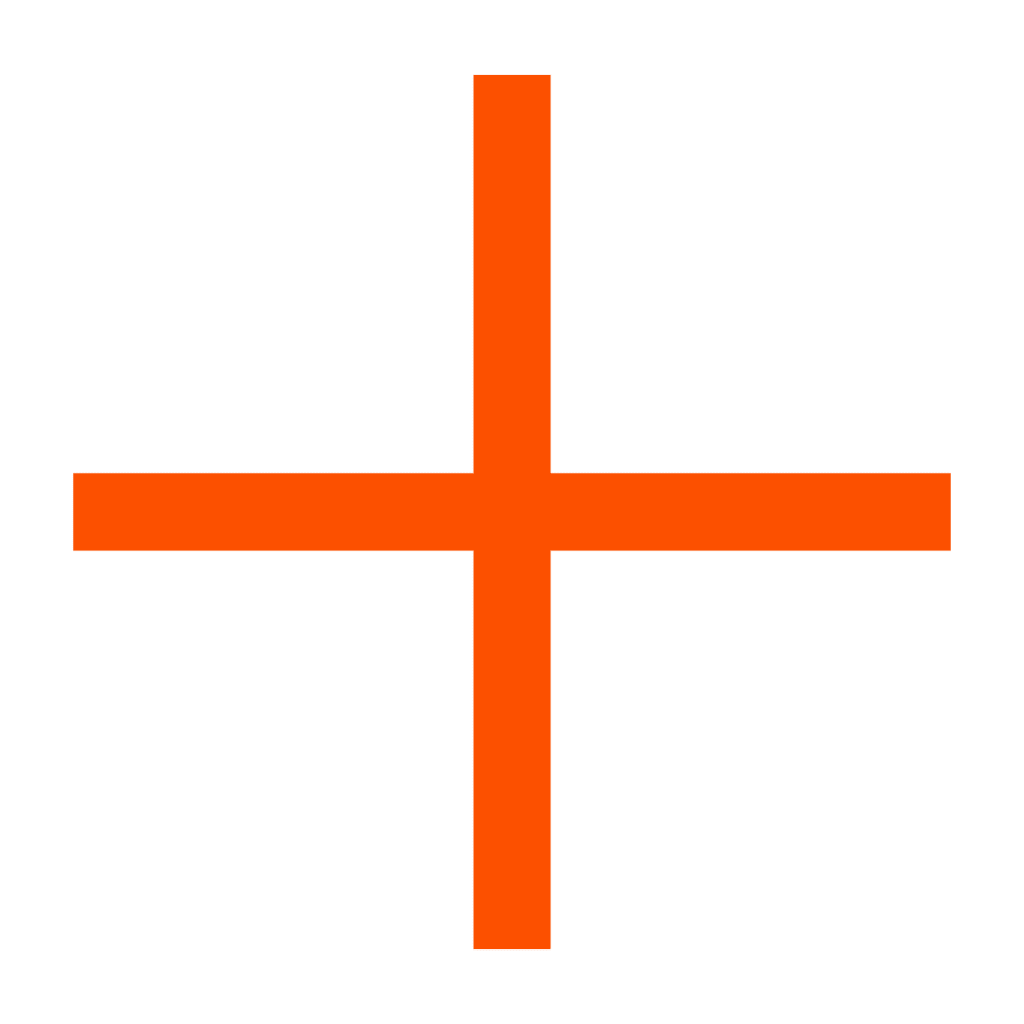
Programmable PhotoPolymerization (P3) technology, an evolution of digital light processing (DLP), is ushering in a new era in 3D printing - the mass production of functional end-use parts.
P3 software precisely orchestrates light, temperature, pull forces and pneumatics to optimise prints for the best possible results. With P3, manufacturers can achieve injection moulding part quality and surface finish with incredible accuracy, in a diverse and continuously growing range of high-performance materials.
With a patented pneumatic separation mechanism and closed feedback loop, separation forces are reduced and faster print times achieved, whilst ultra-fine features and an expanded range of geometries are available with incredible accuracy.
Stratasys perfect existing technique with P3
With the addition of advanced materials, the system is based on digital light processing (DLP) technology which drives the printer head precisely over the build platform to build layers of accurate and consistent precision into soluble photopolymers, resulting in an ultra-precise 3D print that is highly functional and durable.
What makes P3 unique?
The ability to print flexible parts made of clear photopolymers on a conventional 3D printer means you only need one machine to produce both rigid and flexible objects with the same quality.
Gated-based layer-by-layer manufacturing process efficiently directs UV light and oxygen through soluble photopolymer material to cure its components during fabrication.
OpenAM software provides developers, researchers and early adopters with advanced tools to develop and experiment with new materials and custom workflows.
Get critical physical insights early in the design process to streamline development cycles and accelerate time to market, with the best possible final product.
Parts can be produced with very fine features and smooth surface finishes that enable further finishing steps such as injection moulding and bonding.
The ability to use a variety of different thermoplastic resins lets you quickly prototype designs mimicking metals, glass and other materials for a wide range of industrial applications.
How P3 works:
Five critical parts of the P3 process enable the unique combination of high throughput, production-grade part quality and materials.
Light
Programmable light sets off an exothermic reaction that forms layers with outstanding resolution, accuracy and dosage control.
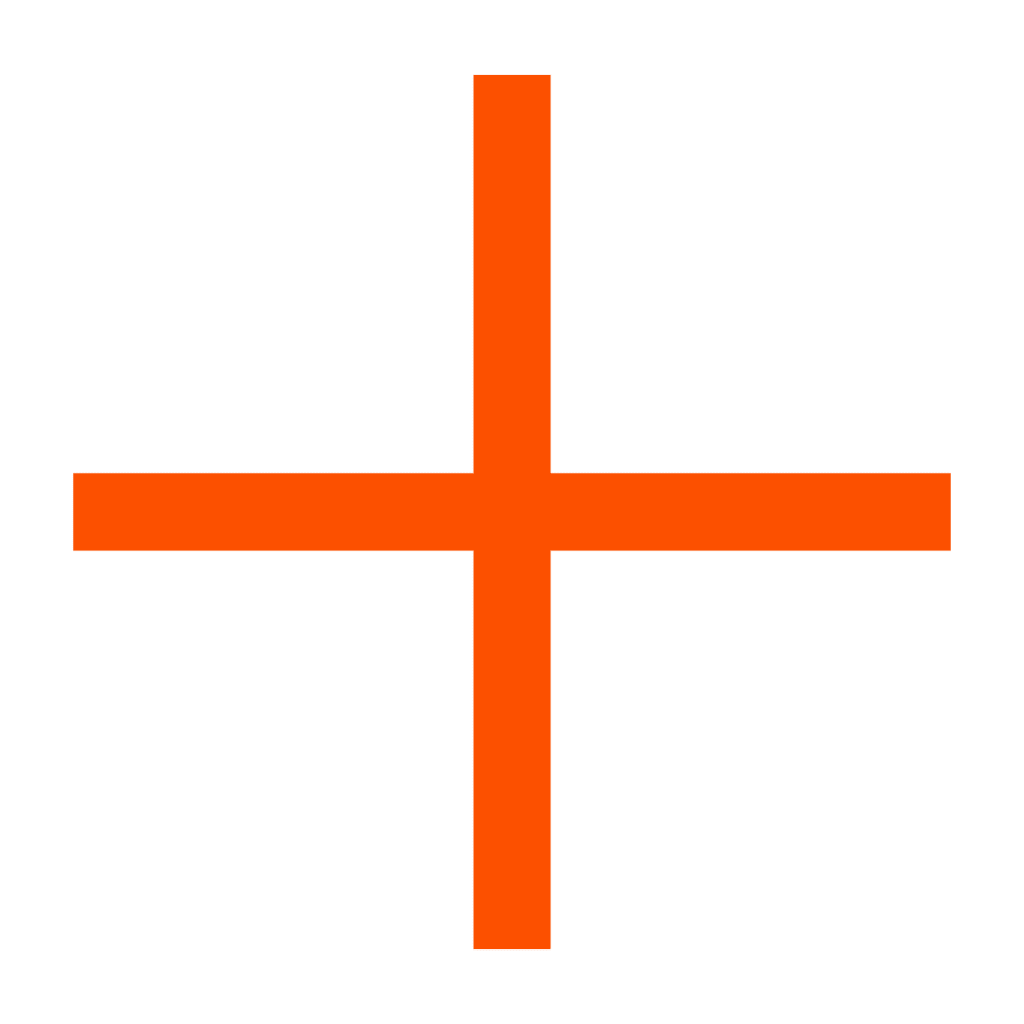
Environmental stability
Temperature-controlled printing mitigates warping and shrinkage, while unlocking materials with advanced properties, like flame retardancy.
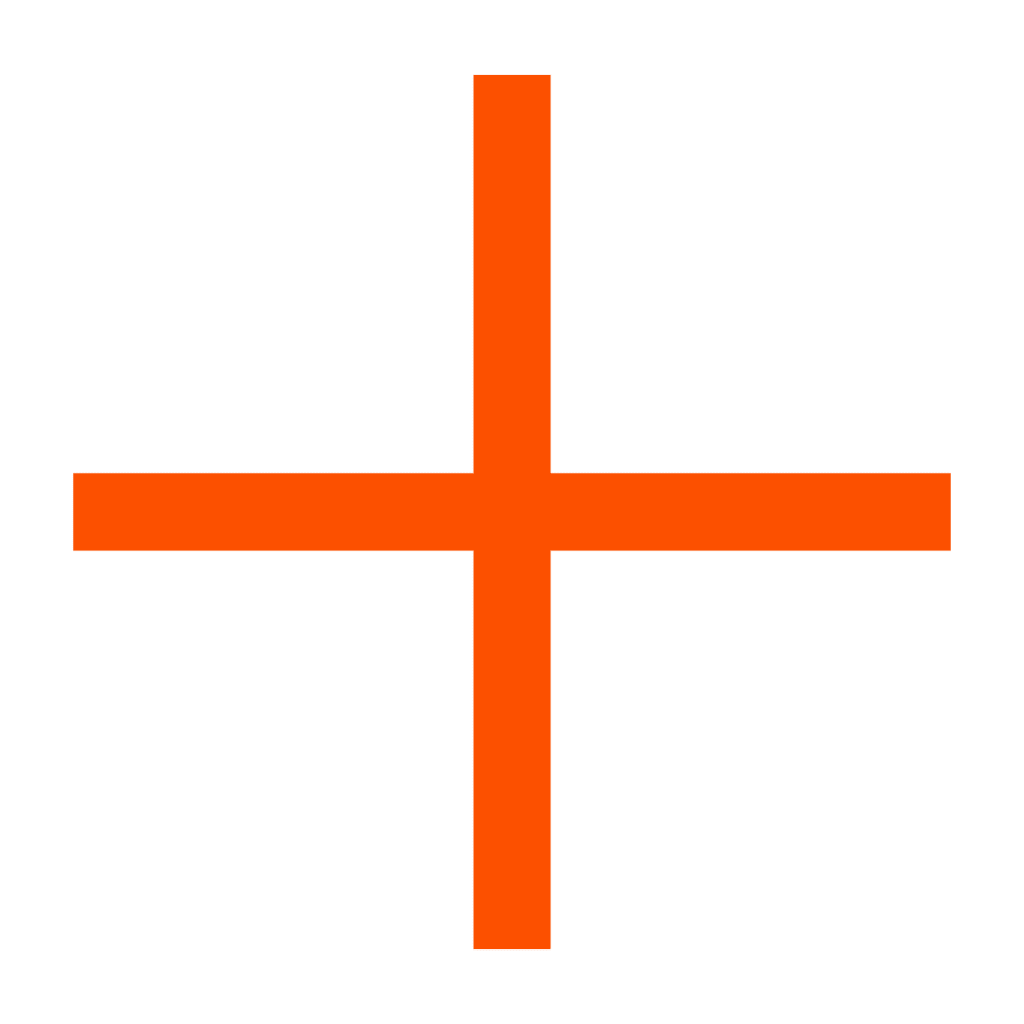
Pneumatic separation
A perfectly timed separation procedure reduces pull forces, leading to a moulded-like surface finish, high throughput and ultra-fine features.
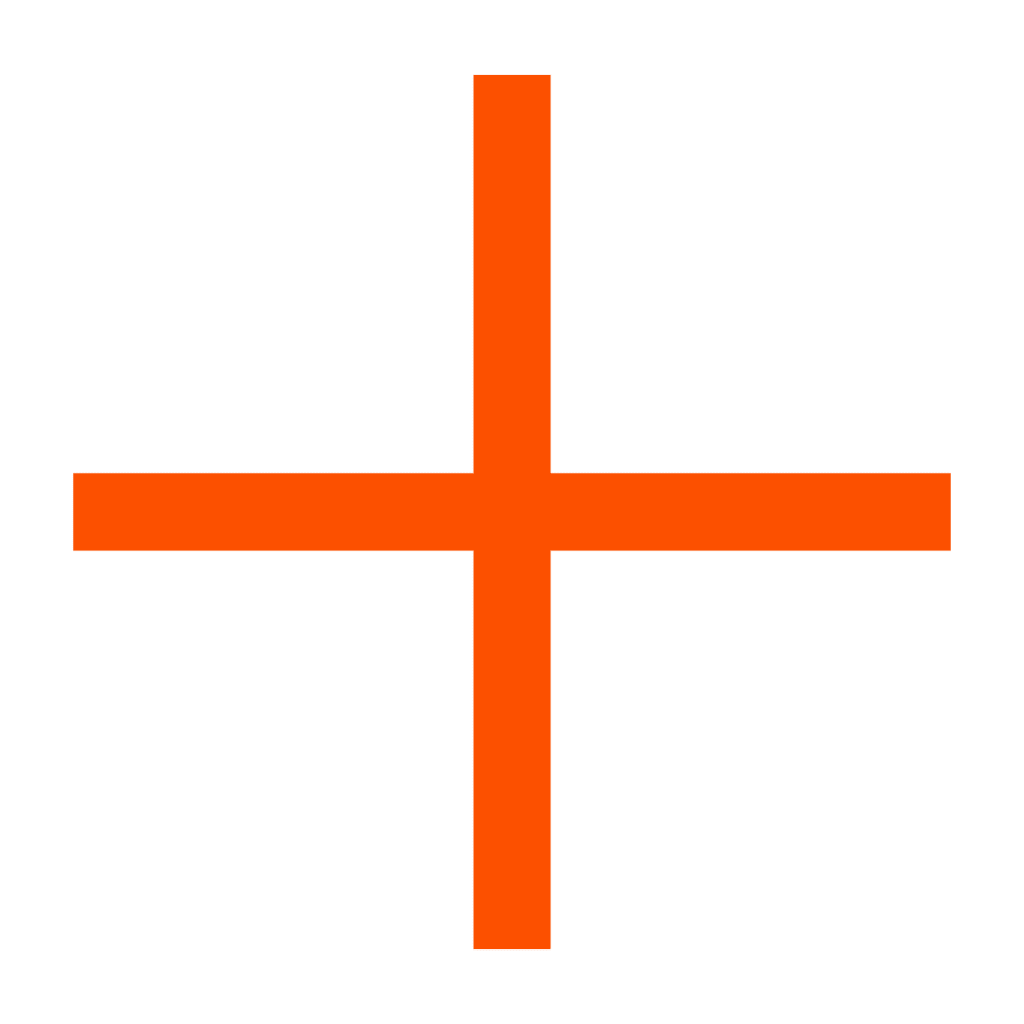
Motion
Precise control over printer movements ensures a repeatable, fast and accurate workflow in a wide range of geometries and performance materials.
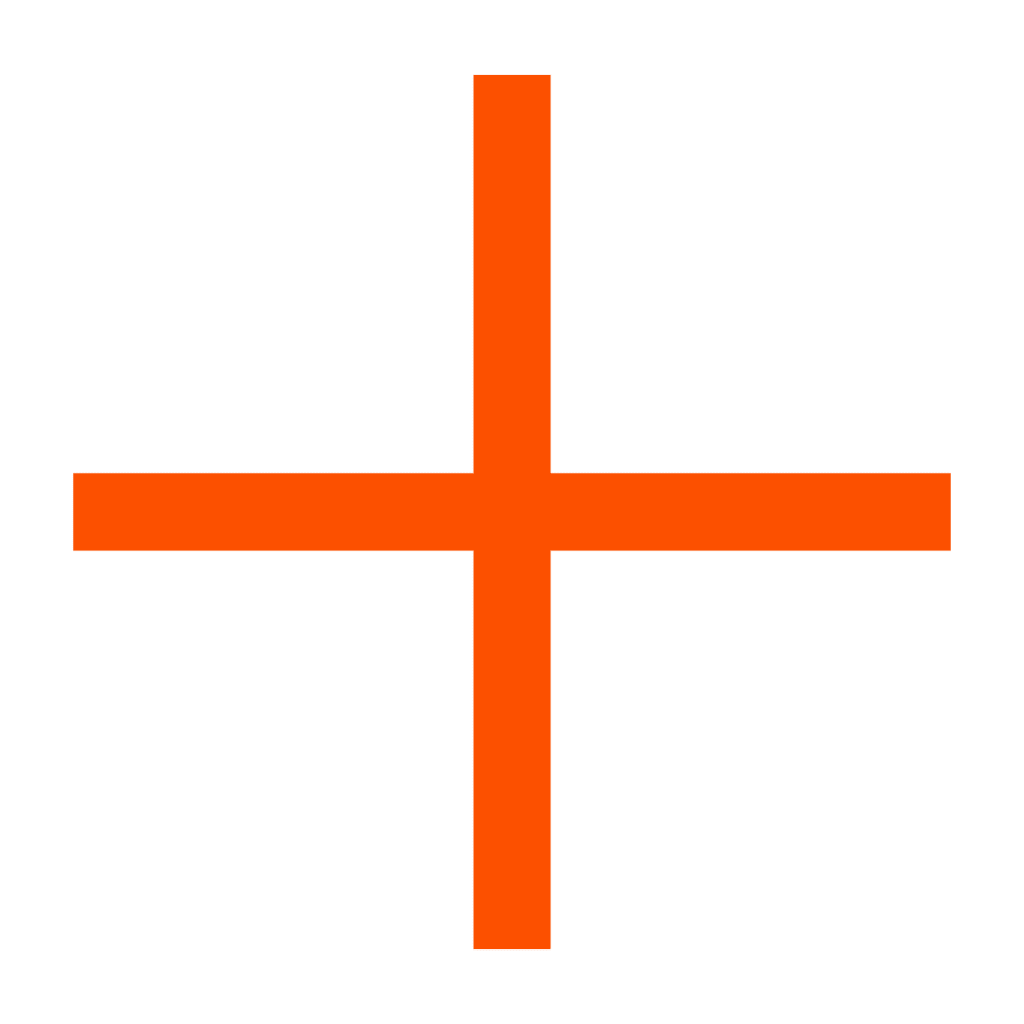
Green strength
The P3 process produces a high polymerisation conversion, unlocking faster print times, extreme geometries, and build nesting.
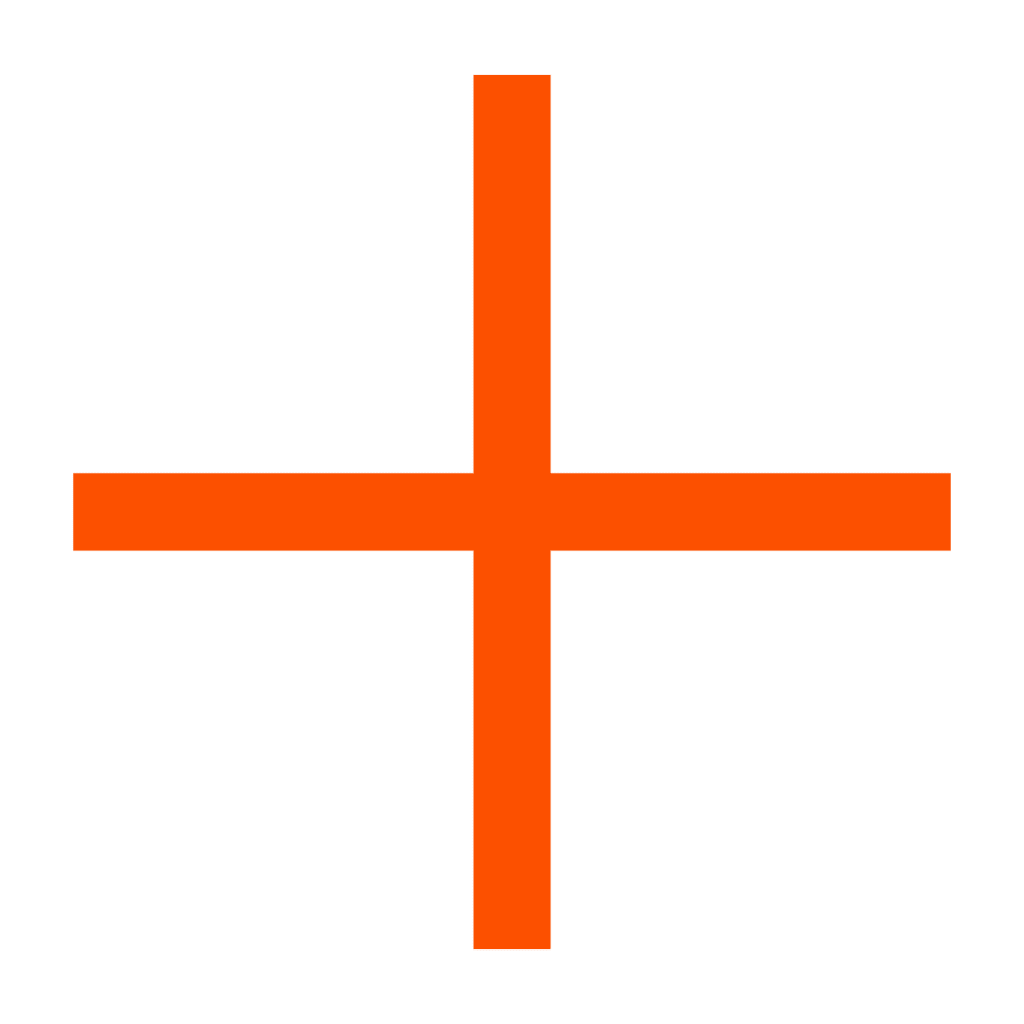
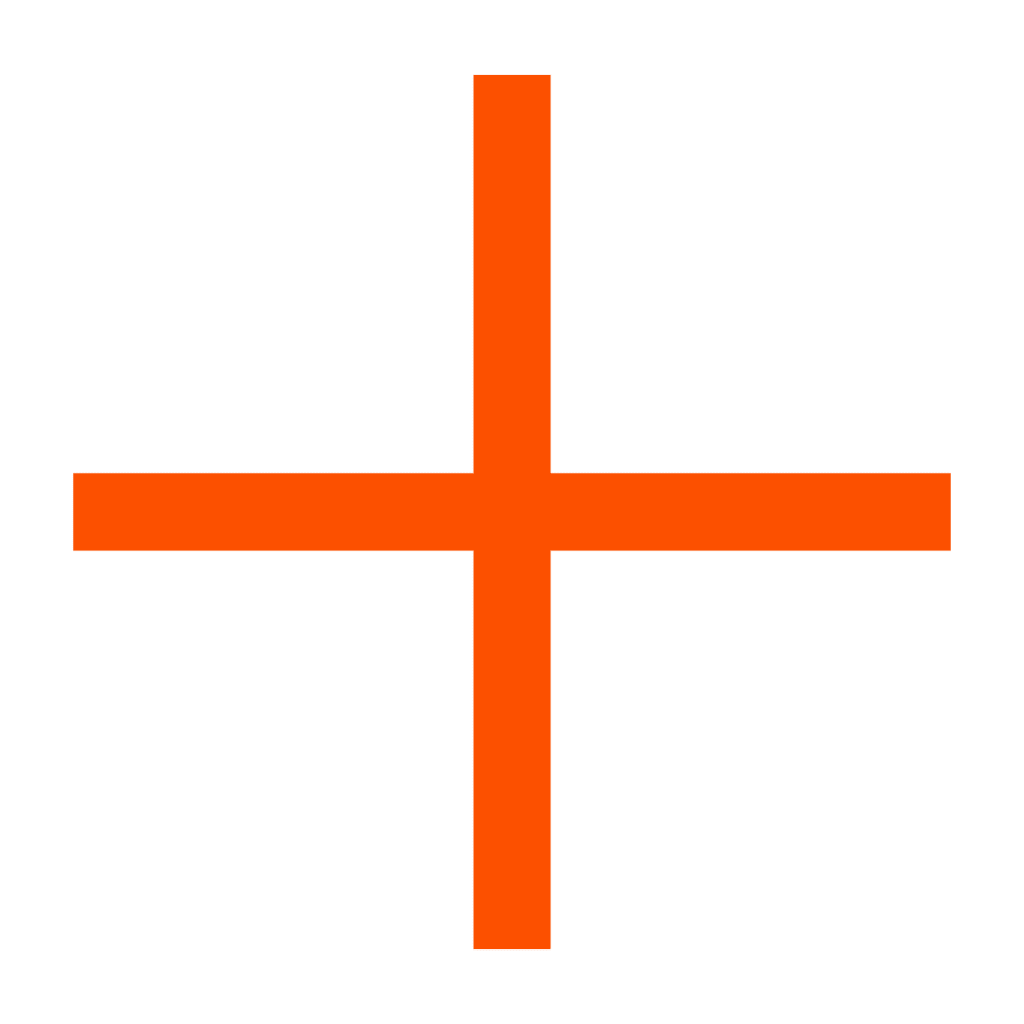
Accurate, repeatable, isotropic.
P3 cures using UV light and oxygen. This makes it super accurate and very consistent, as the resin doesn’t move around much. Also the O2 helps to keep the temperature stable and prevent the resin from heating up too much and cracking.
OML: Greater control
Open Material License allows for downloading of supporting files. This allows the manufacturer to provide specifications and materials used to manufacture the product, giving the customer more control in the 3D printing process. It also allows the manufacturer to market their product to a wider audience with the ability to customise or redesign their part to fit specific uses and designs.
Programmable PhotoPolymerization: Unlocking new materials, features and applications
Automated programming that simultaneously controls process conditions and photopolymerisation enables significant advancements in both the performance and reliability of photopolymer processing systems. For example, the ability to program and monitor multiple photopolymer solutions enables cost-effective implementation of systems that include diverse materials to optimise material performance and reduce total system cost. Programming also allows the system to accurately execute multi-step processes to achieve complex specifications at low cost.
P3 FAQs
After printing is completed, the object must be removed from the printer support material and cleaned of support material and resin. A final post curing process is required, utilising a UV light box. Post-processing can also involve painting or applying a coating to the surface to protect or enhance its appearance.
Programmable PhotoPolymerization or P3 3D printing is a new technology that can print faster and with greater accuracy than traditional 3D printers. Speeds can vary depending on the size of the object being printed but are typically much faster than traditional 3D printers with the ability to print multiple objects at the same time.
Programmable PhotoPolymerization or P3 3D printing is extremely accurate with the ability to print objects with very fine detail, ideal for applications where tight tolerances are required to produce functional parts. P3 technology can also be used to create patterns or moulds for investment casting which results in very accurate parts with smooth surfaces.
Programmable PhotoPolymerization or P3 3D printing uses a light sensitive material called a photopolymer which is cured when exposed to light from a projector below the build platform. Once the object has been formed it is removed from the build platform ready for the next part to be printed.
Programmable PhotoPolymerization or P3 3D printing can produce large objects up to 192 x 108 x 370 mm, an advancement on DLP technology. It is also possible to build multiple smaller objects on one build platform, giving you verstaility within your print workflows.
Programmable PhotoPolymerization or P3 3D printing has a very high resolution of around 50 microns which means that the details in an object will be very crisp with no blurriness at all.
P3 3D printing is cost-effective for producing medium to large-scale production volumes, offering a low-cost alternative to traditional manufacturing methods and a quick turnaround between design and production. The return on investment is typically achieved within three to six months depending on the application.
There are a number of industries that benefit from using P3 3D printing including aerospace, automotive, medical, defence and oil & gas in which accuracy and reliability are of paramount importance.
– For production of prototypes and mechanical parts that require high strength and light coloured finishes we recommend the use of tough rigid resins.
– When designing products for clinical applications it is important to use biocompatible materials which are easy to clean and sterilise. For these types of applications we recommend using our flexible resins which are also easy to wipe down between prints.