What is FDM 3D printing?
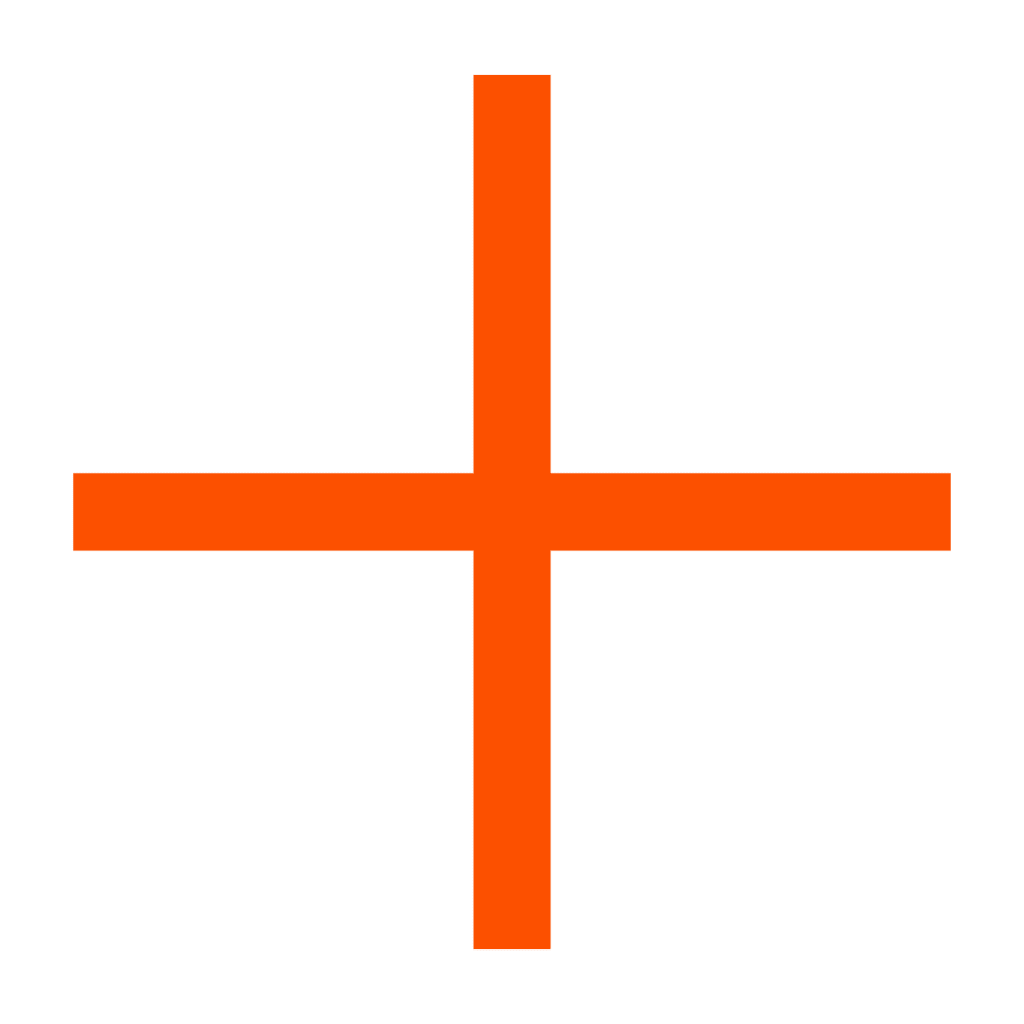
Fused deposition modelling (FDM) printing builds parts layer by layer from the bottom up, by heating and depositing thermoplastic filament.
A technique invented by Stratasys more than 30 years ago, FDM is popular among modern manufacturers seeking flexible alternatives to traditional production, for example, where fabrication is extremely time-consuming, tooling is expensive and achieving complex shapes is difficult.
FDM uses engineering-grade thermoplastics to create accurate, repeatable, environmentally stable, lightweight but high-strength shapes faster than ever before, reducing waste and energy usage in the process.
Prints are tough enough to be used as advanced conceptual models, functional prototypes, manufacturing tools and production parts.
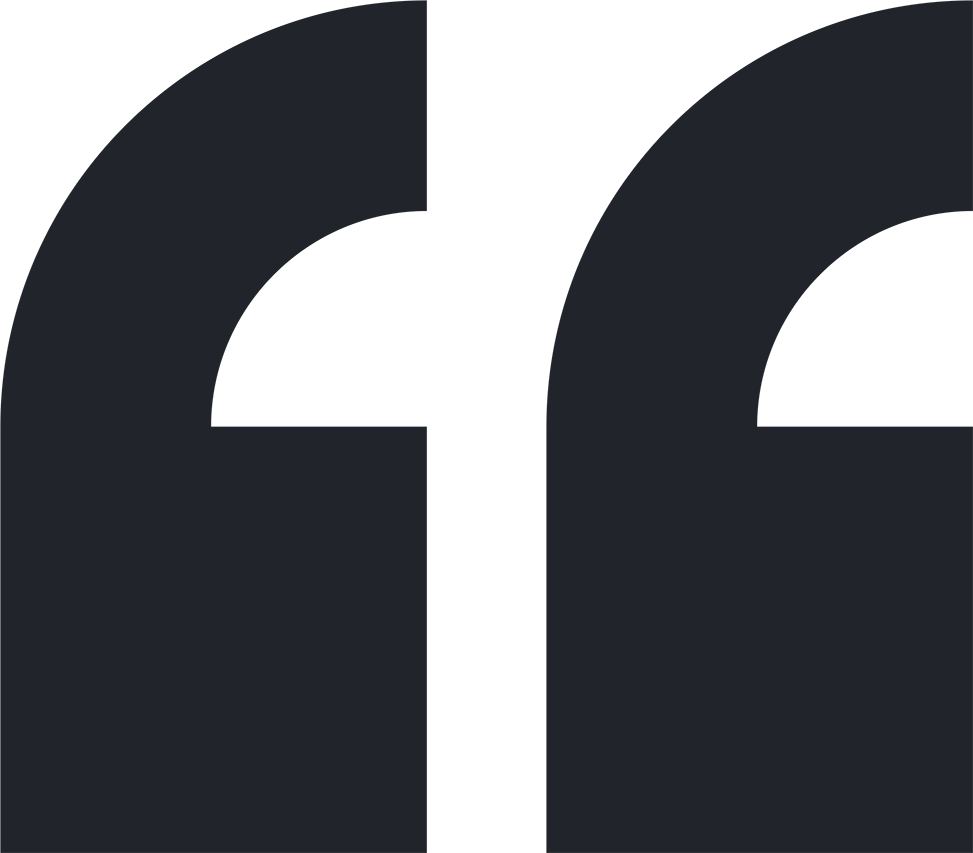
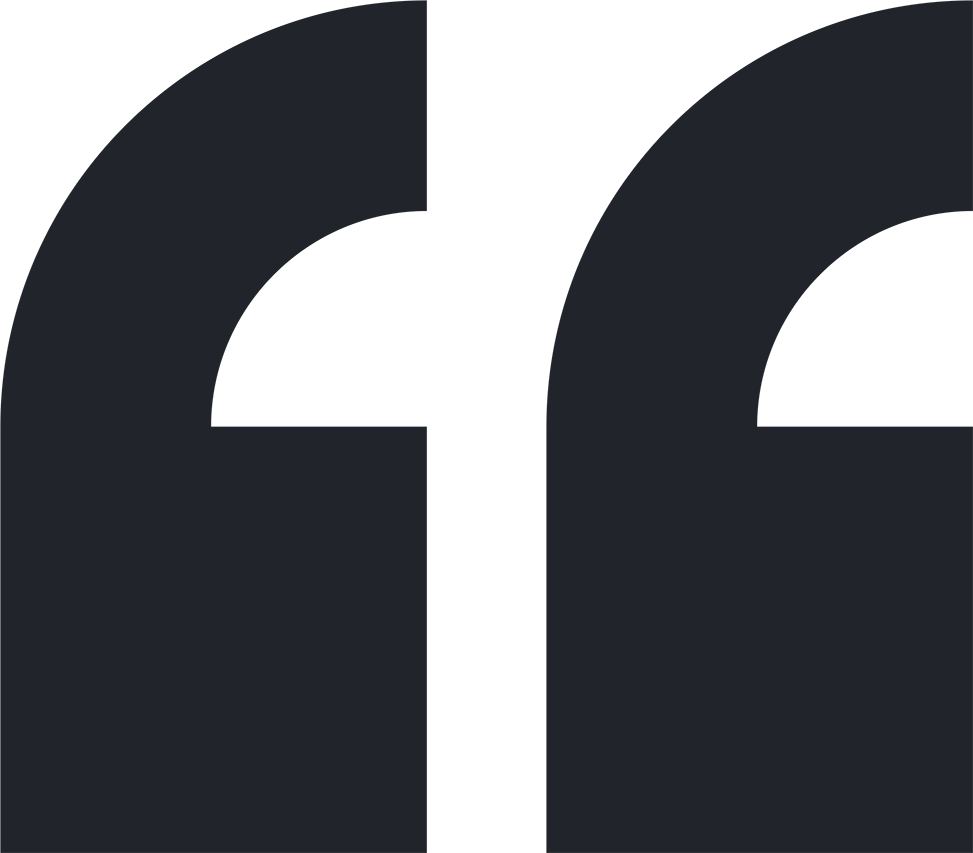
FDM is really the king of all 3D-printing processes. It’s here to stay – there’s no other process which is safer and more reliable in general.
Jake Augur - Fluxaxis
The benefits of FDM
Cost-effective
A cost-effective method for printing functional prototypes, manufacturing aids and high value, low volume projects.
Speed
Parts can be printed in just hours, meaning lead times are short compared to traditional manufacturing in which parts can take days, if not weeks to become available.
Flexibility
Ideal for custom tooling, jigs and fixtures, which means you can switch between projects faster than ever before and at a fraction of the cost.
Accuracy
Well suited to critical components including those with superior finishing, tight tolerances and mechanical properties.
Precision
Strength
Large build capacity
Material variety
Rapid turnaround
Part production
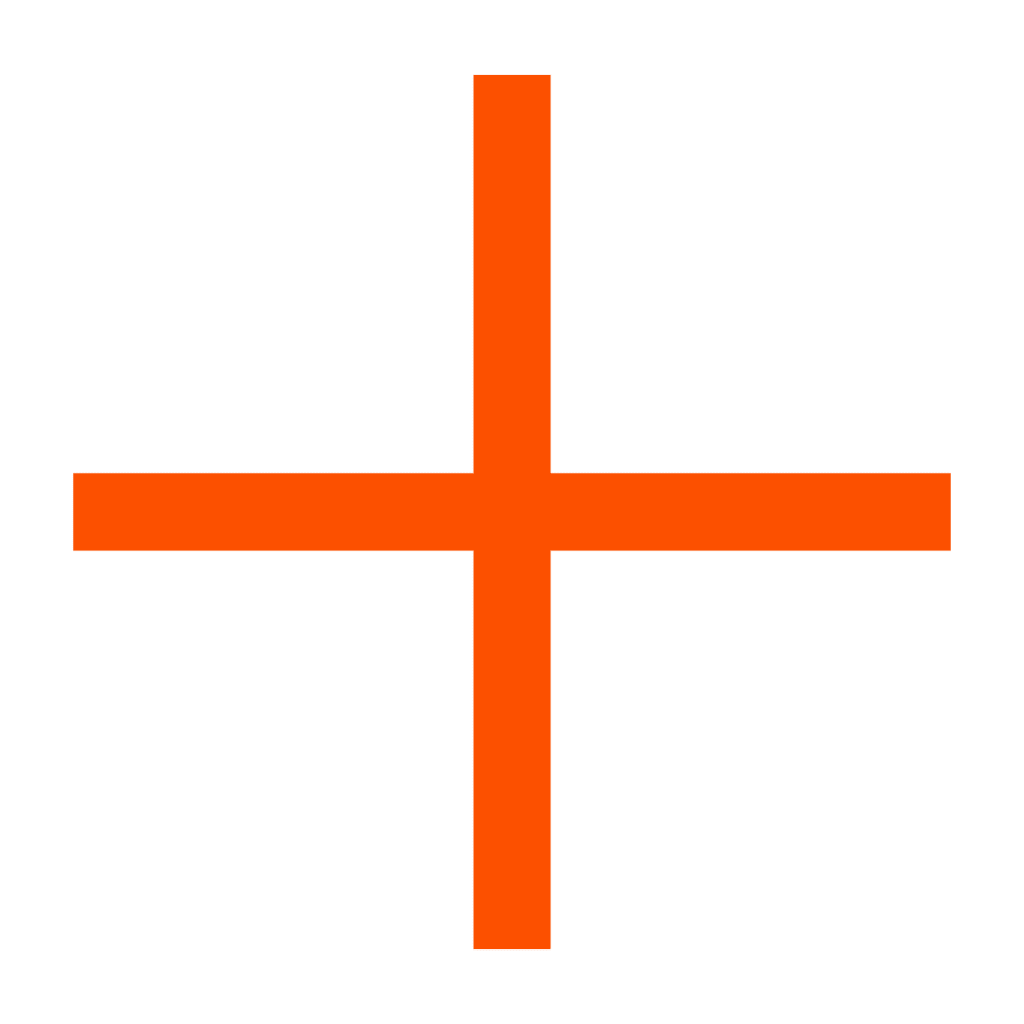
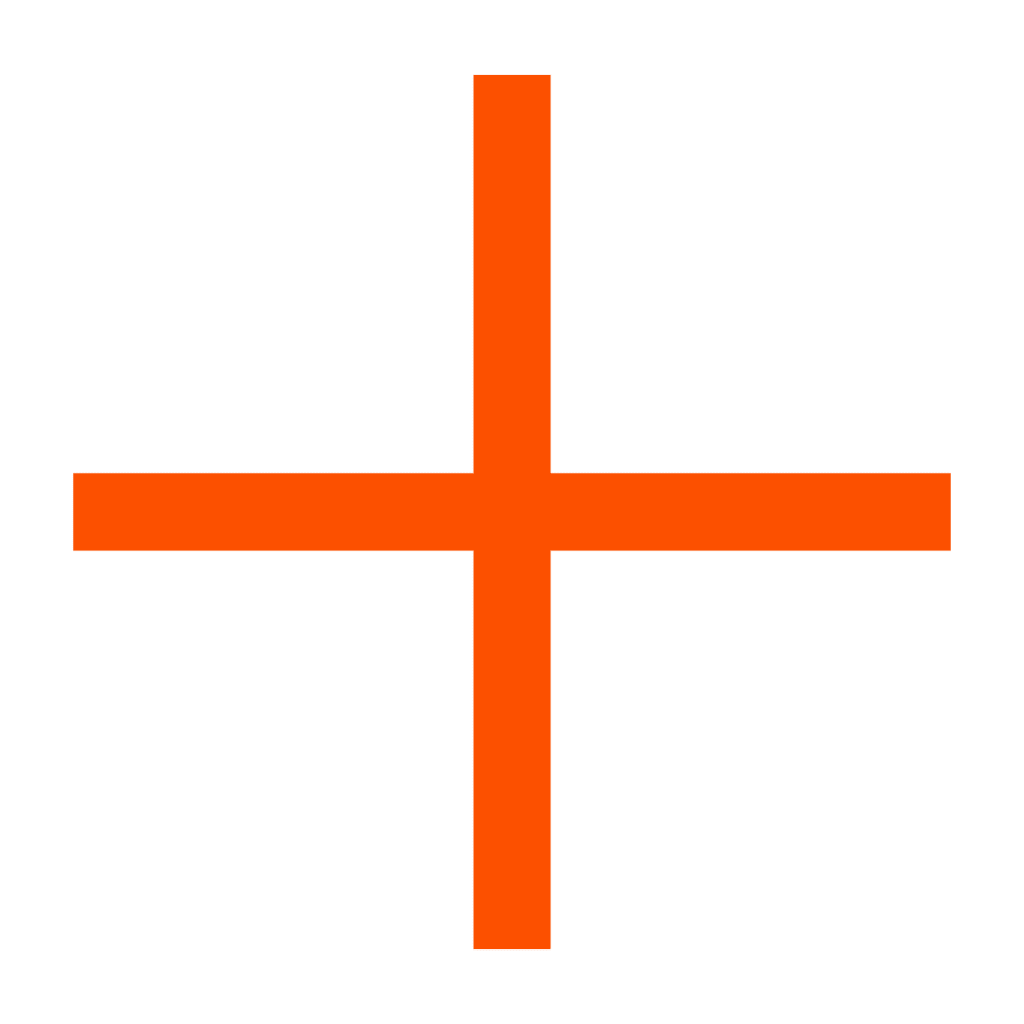
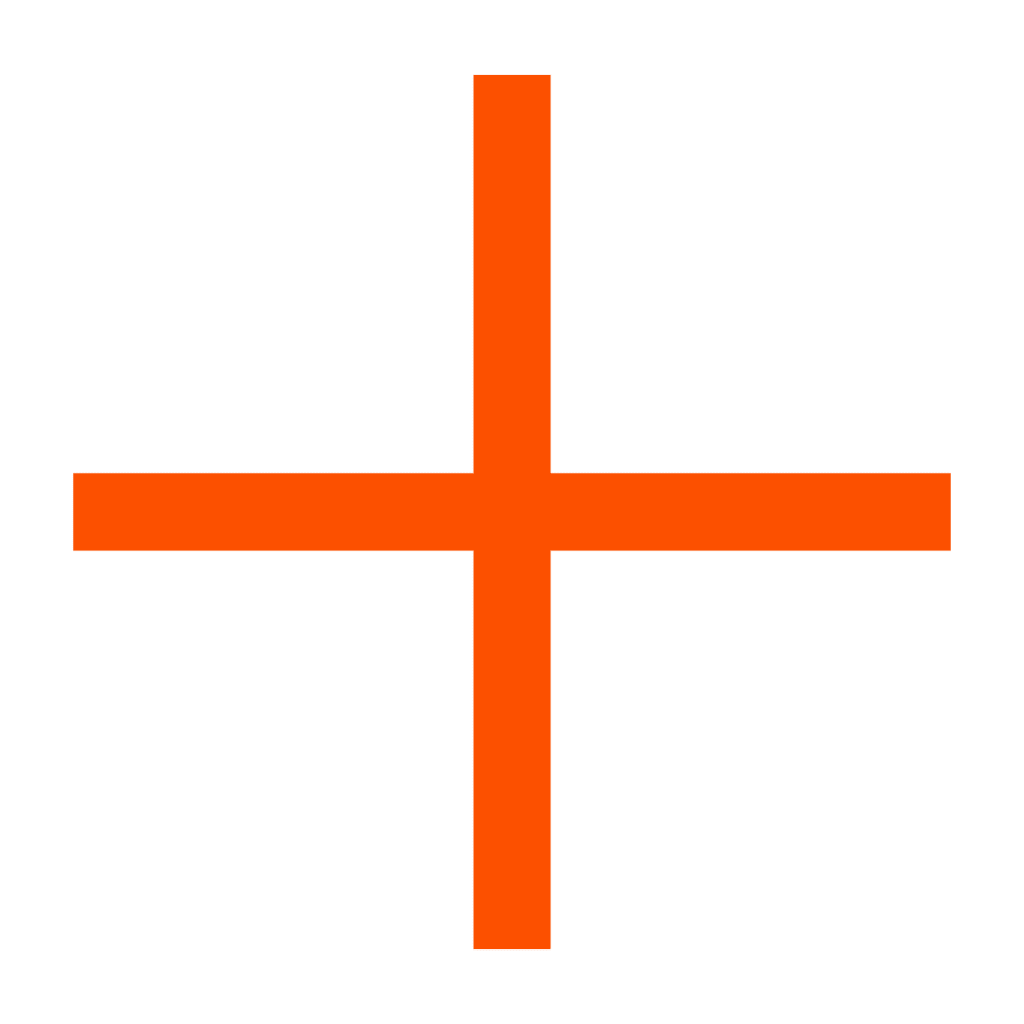
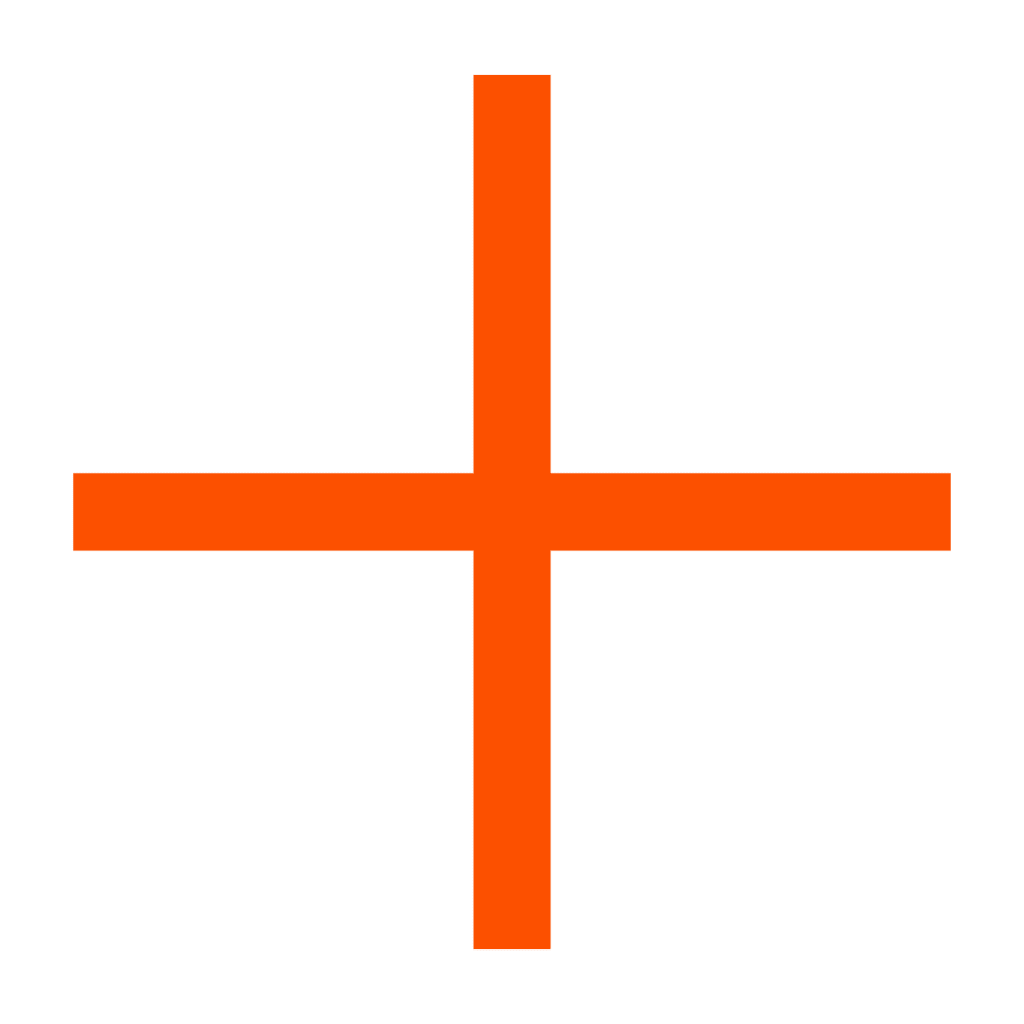
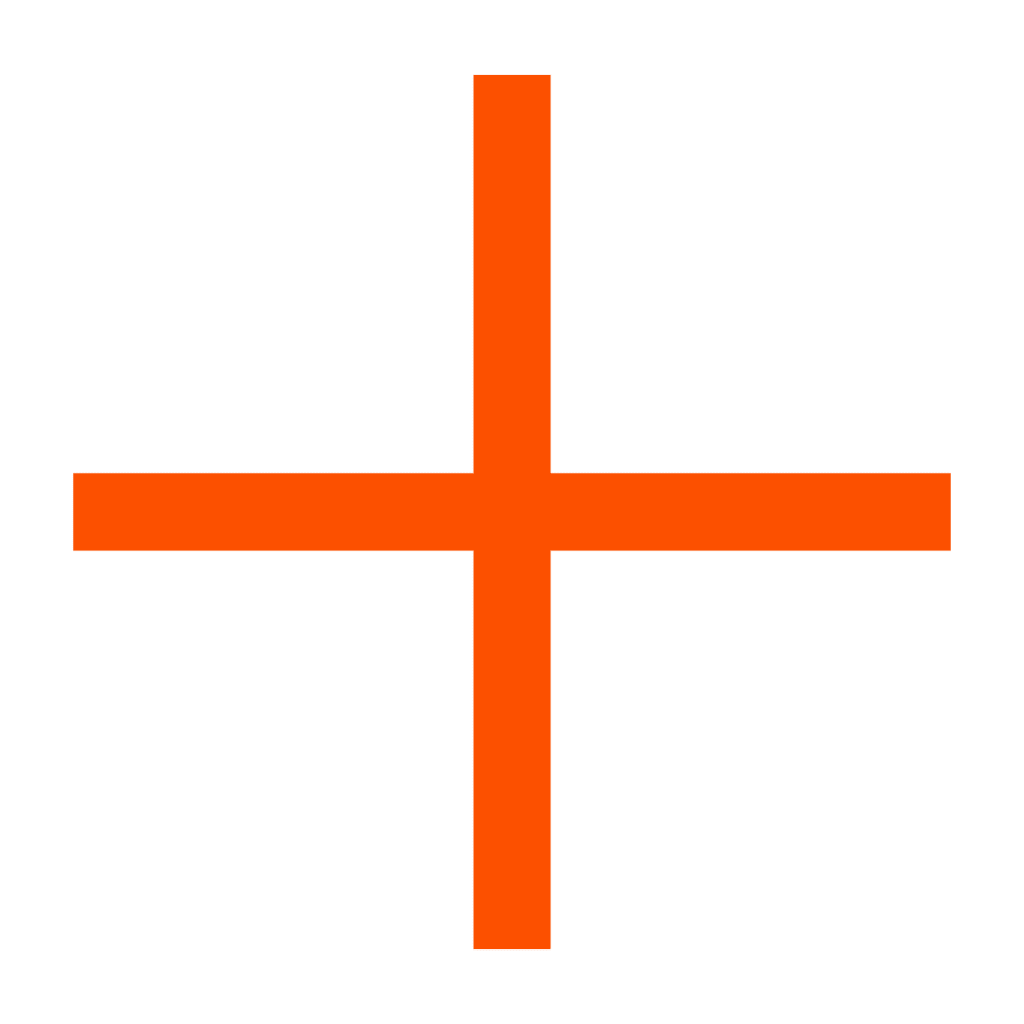
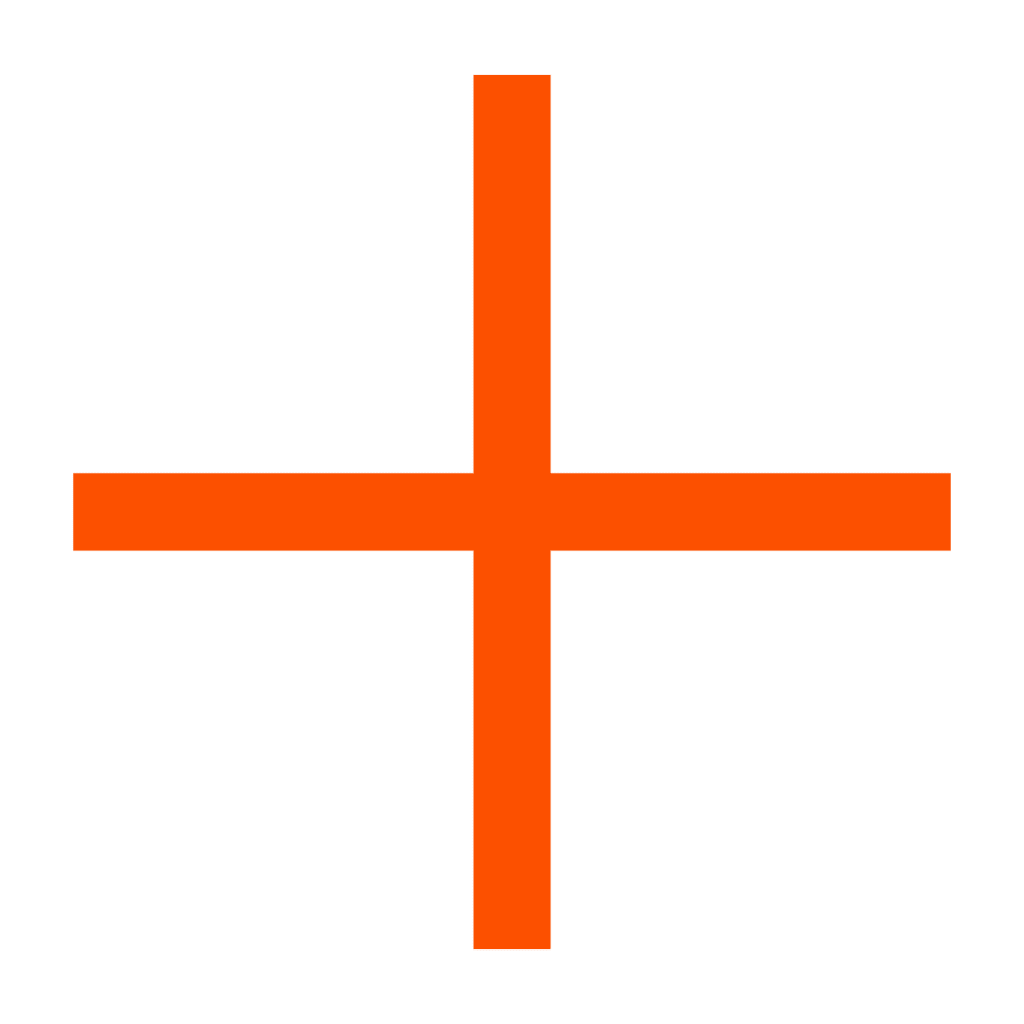
FDM desktop & industrial:
A size and shape for every scenario
No matter if you are planning on large builds at small volume, small builds at large volume and everything in between, Stratasys FDM 3D printers serve every scenario. From desktop to industrial FDM printers, you can find the right model that satisfies all builds, briefs and budgets.
The main difference between industrial and desktop FDM printers is in the scale of production. Most desktop FDM 3D printers are used to create prototypes while industrial FDM printers are designed to create end-use parts, jigs, fixtures and workholdings, as well as functional prototypes.
Industrial scale printers offer greater scalability, repeatability and accuracy. They will offer a much larger build envelope, allowing the creation of large parts, and have a much wider range of materials available and compatible with them; often materials that offer high-tensile strength and heat resistance properties like ULTEM 1010 resin and Nylon 12 Carbon Fibre.
How does FDM work?
Thermoplastic polymers come in filament form and, using the FDM process, are extruded and built layer by layer to build highly-functional parts. CAD files that are pre-loaded into FDM 3D printers with dimensions automatically loaded are easily exportable with GrabCAD to ensure 3D printing at the touch of a button.
When the nozzle hits the correct temperature for the material, the fused deposition modelling printer extrudes the filament through the extrusion head and nozzle, distributing filament layer by layer, repeating the process before cooling the material until it is solid.
Uses of FDM
Excelling in speed and product testing, the use of FDM in rapid prototyping is common. Due to an ability to create complex parts with complex geometries and process parameters, while retaining a quality surface finish, engineers can test parts with the same or similar properties to the final product, meaning creating an FDM model or prototype is easier than ever.
FDM manufacturing is also a growing subsector, with mechanically-critical parts often getting made in low to medium volumes using fused deposition modelling. The wide range of available materials with high strength and heat resistance also make FDM a popular choice, particularly in the automotive and aerospace industries in which tolerance and timing are just as important as quality and strength.
FDM FAQs
FDM cuts down and simplifies post-processing considerably compared to other processes. It is often used for advanced conceptual models, functional prototypes and production parts. You can sand, prime, paint and drill in post-processing, and the removal of support materials is straightforward with FDM. You can break off support material before reaching the cleaning station to speed up the process and allow your WaterWorks solution to last longer.
FDM is the best technology for building large parts. There is less waste created and it is much more affordable to create large parts with FDM over any other process. Print stages for FDM 3D printers vary considerably with some desktop models having a maximum build envelope of 200x200x200 mm, while the maximum build envelope on an industrial model is considerably more at up to 900x600x900 mm. The spacious build envelope on the Stratasys F770 for example is one of the biggest and best in the industry.
FDM 3D printing is inexpensive when compared to other 3D printing methods and is a consistently reliable option for strength and repeatability. An FDM 3D printer price varies with office-friendly and industrial options available for a vast range of applications.
Stratasys FDM technology is one of the fastest 3D printing technologies in the market today. It can extrude 100 mm of filament every hour depending on part complexity. Speeds can often be adjusted on Stratasys 3D printers depending largely on your specifications. For example, if you want a higher quality, more accurate part you may want to slow the print speed down to 30-40mm/hr, whereas, if speed is the priority, you can ramp up to around 150mm/hr. It is good practice to set a default speed setting and then change it in increments of 5mm/s. There is some trial and error involved in setting your speed but at SYS Systems, we help you make better estimations to save you time and money.
Due to the simplicity of traditional FDM technology, and how easy it is to 3D print parts, it can bring up tolerance challenges. But with Stratasys' heated build chamber technology many of these challenges are eliminated for high-precision parts.
FDM offers an array of materials with different properties, covering all bases from strength to resistance, including chemical, fire and corrosive resistance. ABS, Nylon 12 CF and ULTEM 1010 resin are some widely-used materials in FDM printing when creating parts for spacecraft, aircraft and automotives. FDM Nylon 12 CF (carbon fibre) for example delivers a tensile strength of over 10,000 psi.
Fused deposition modelling 3D printing is simple, cost effective and suited to any volume of parts making it the all-rounder in the 3D printing sphere. The economies of scale on cost per part don’t increase/decrease if you print more. This is one of the major benefits of FDM as you can do one offs or loads unlike with other processes like SAF which requires a higher quantity of parts and/or a full print bed to be cost effective.
FDM allows for the use of hundreds of materials and can create complex parts faster than any other process. For the majority of design, prototyping, tooling and workholding applications, FDM is the technology of choice.
Grow with us:
FDM sample, service and buy
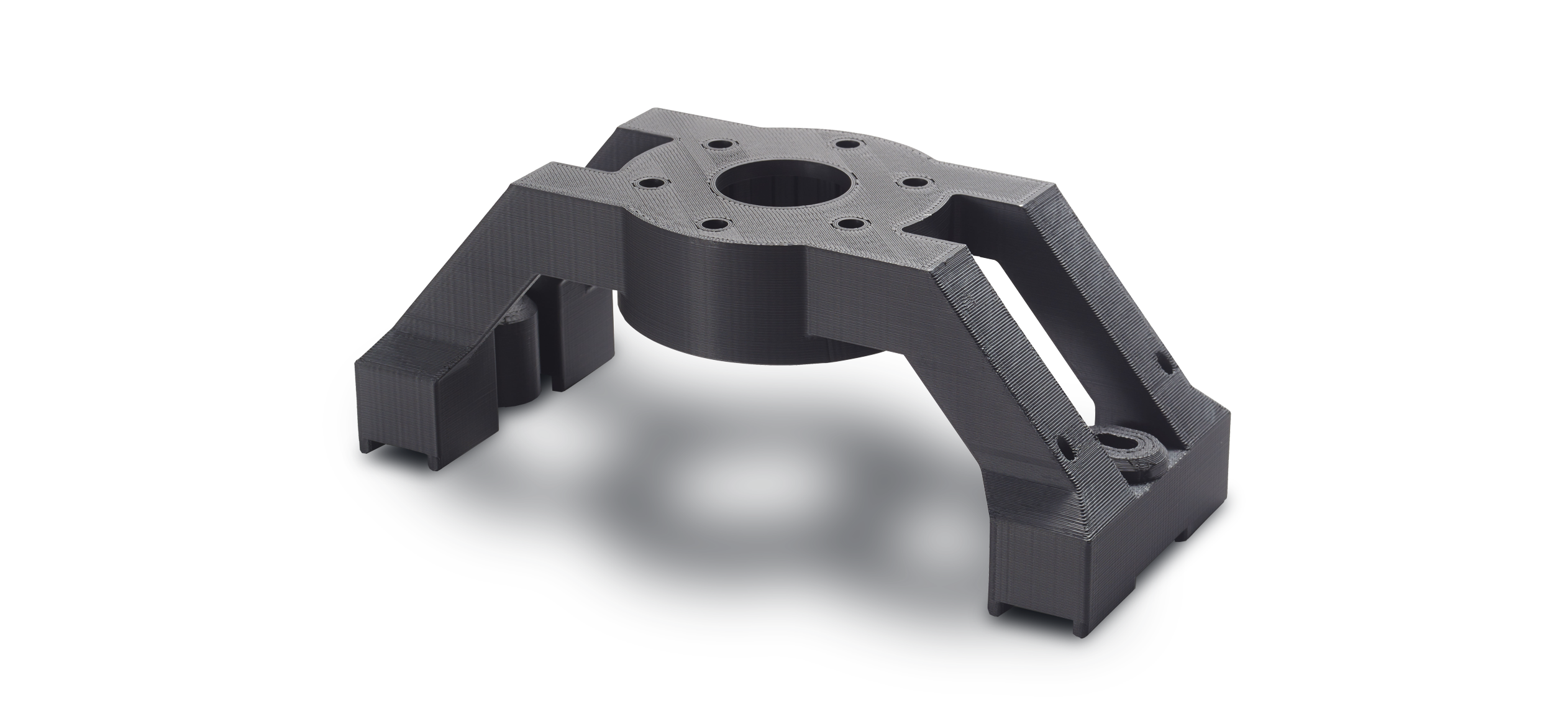
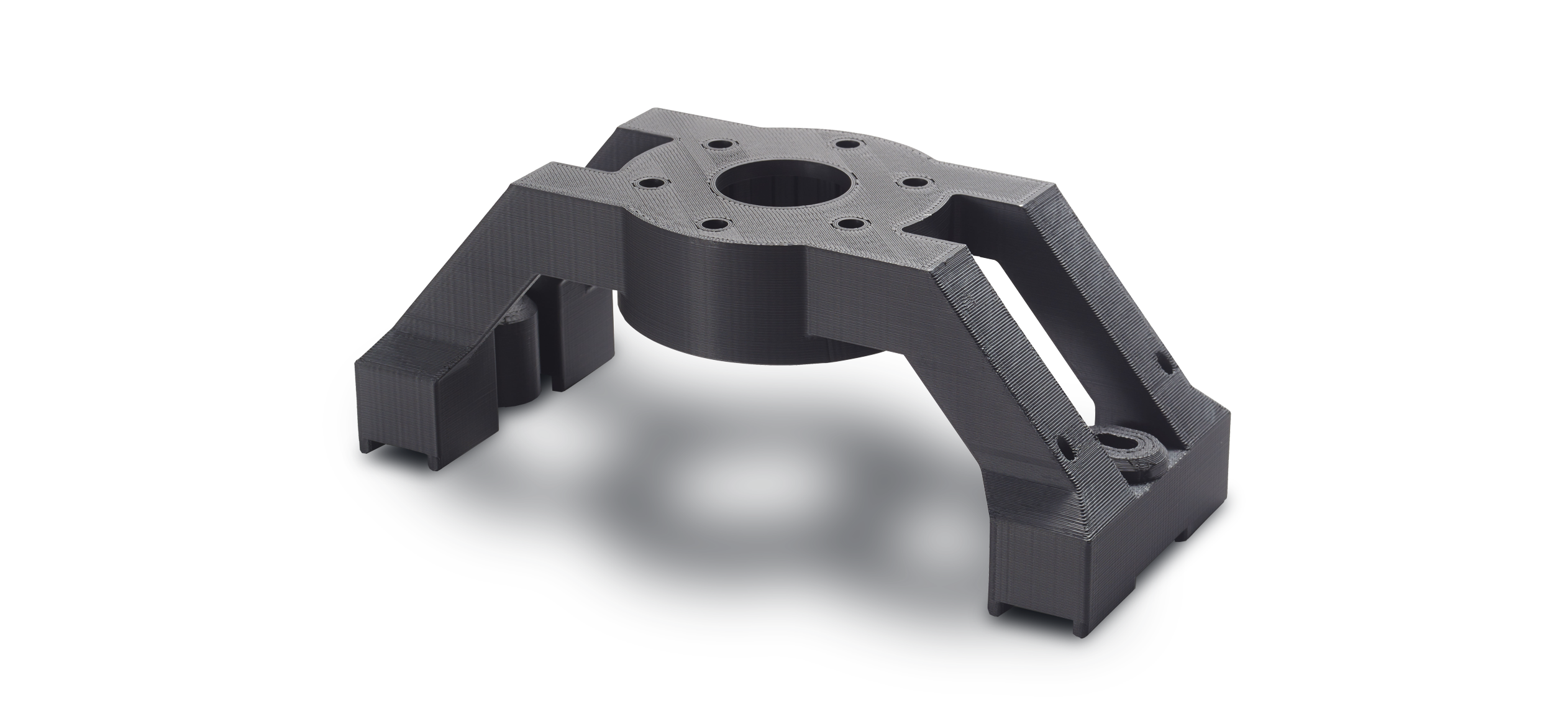
Sample
We offer free sampling of parts and products to suit your needs and applications. Whether you want a sample to mirror the parts you make day-to-day or simply see how additive manufacturing can support your current processes, our team creates quality parts with fast, free delivery. Send your CAD files, and let’s get started.
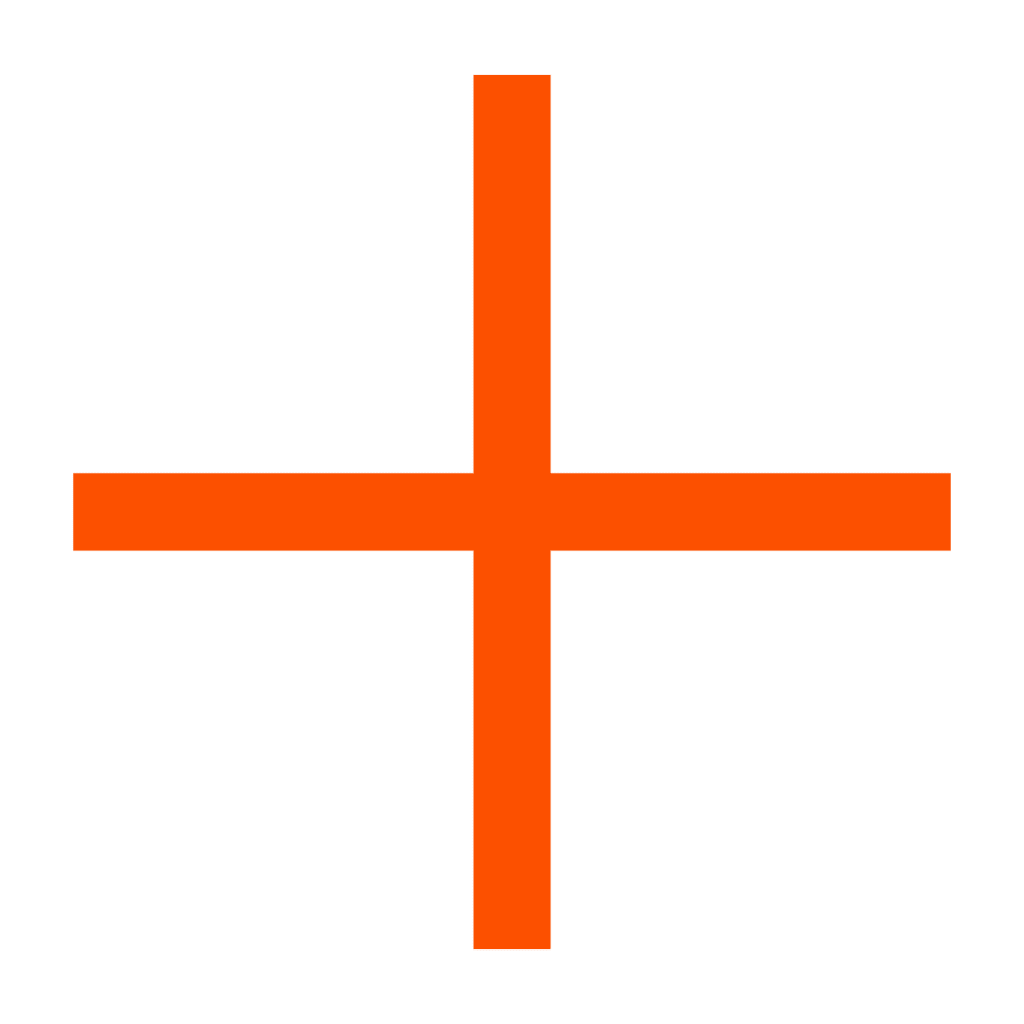
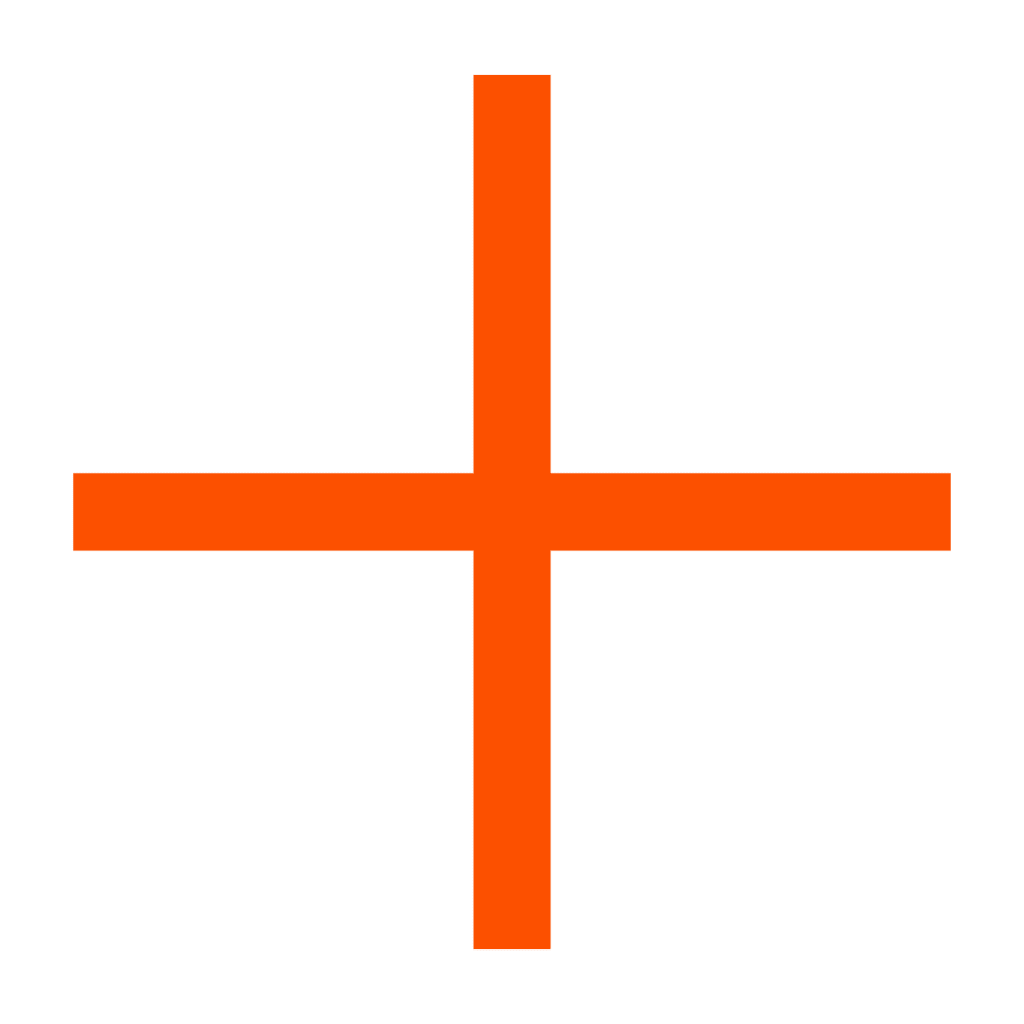
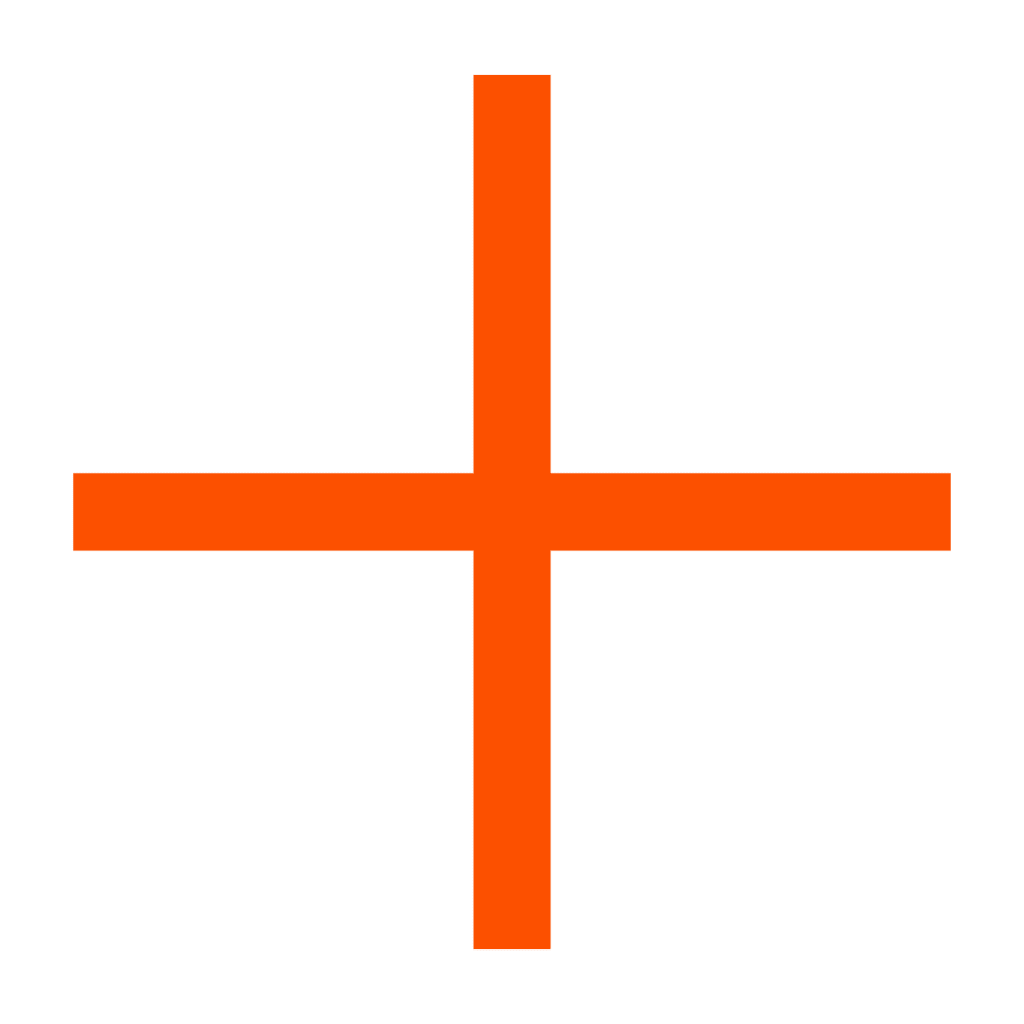
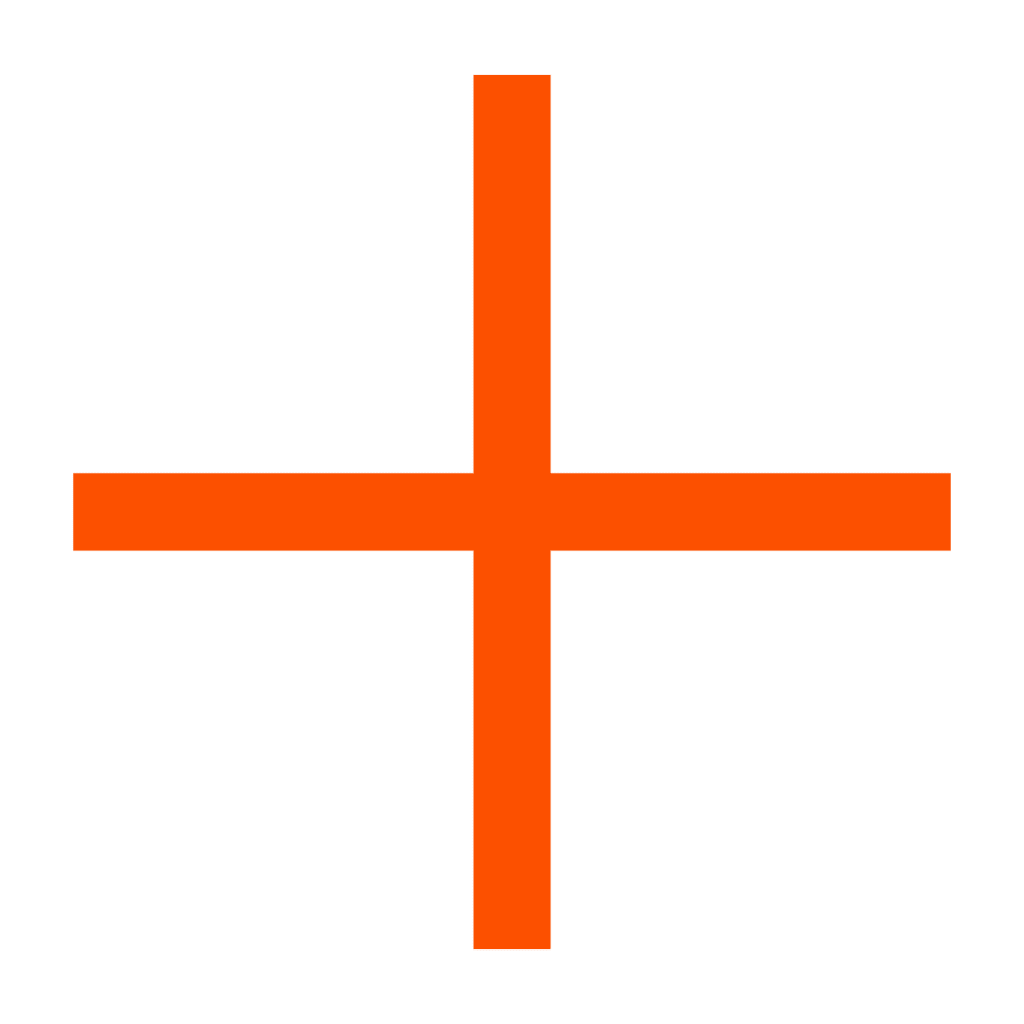
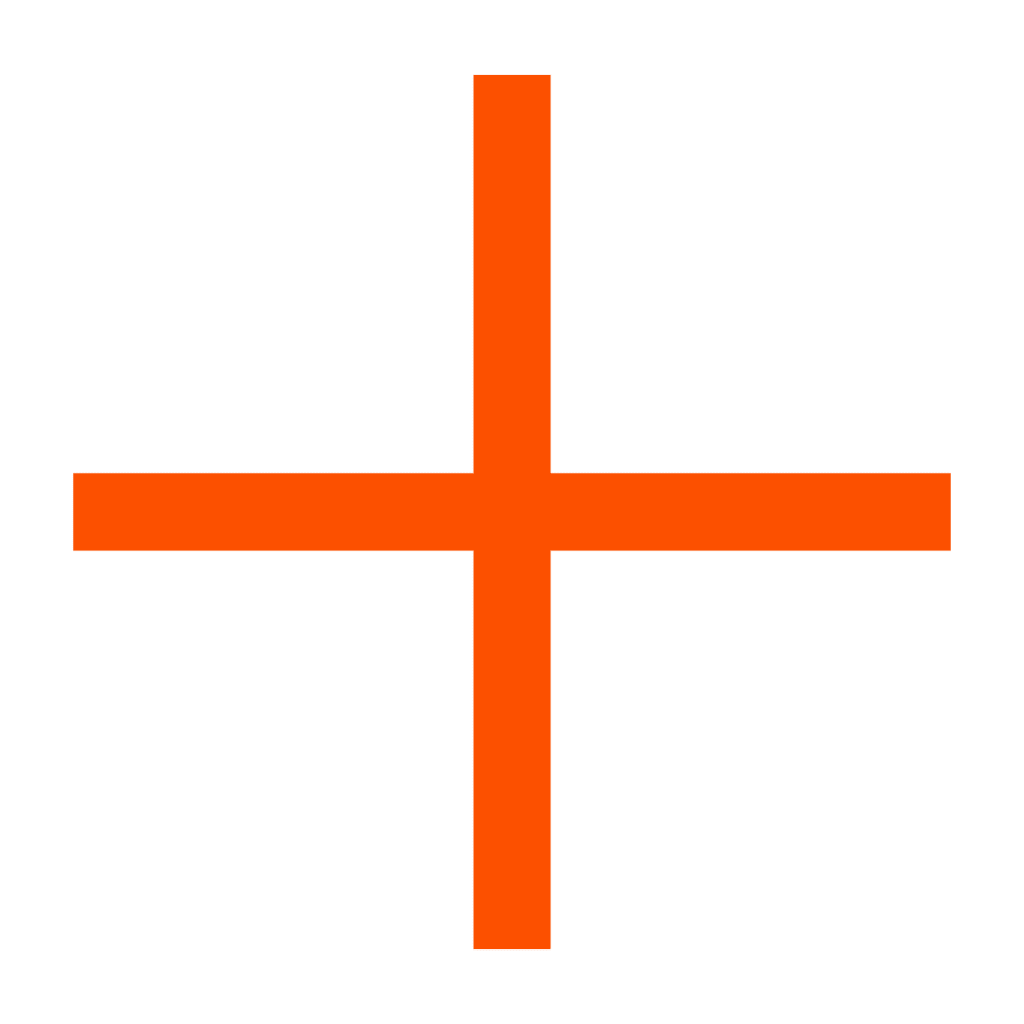
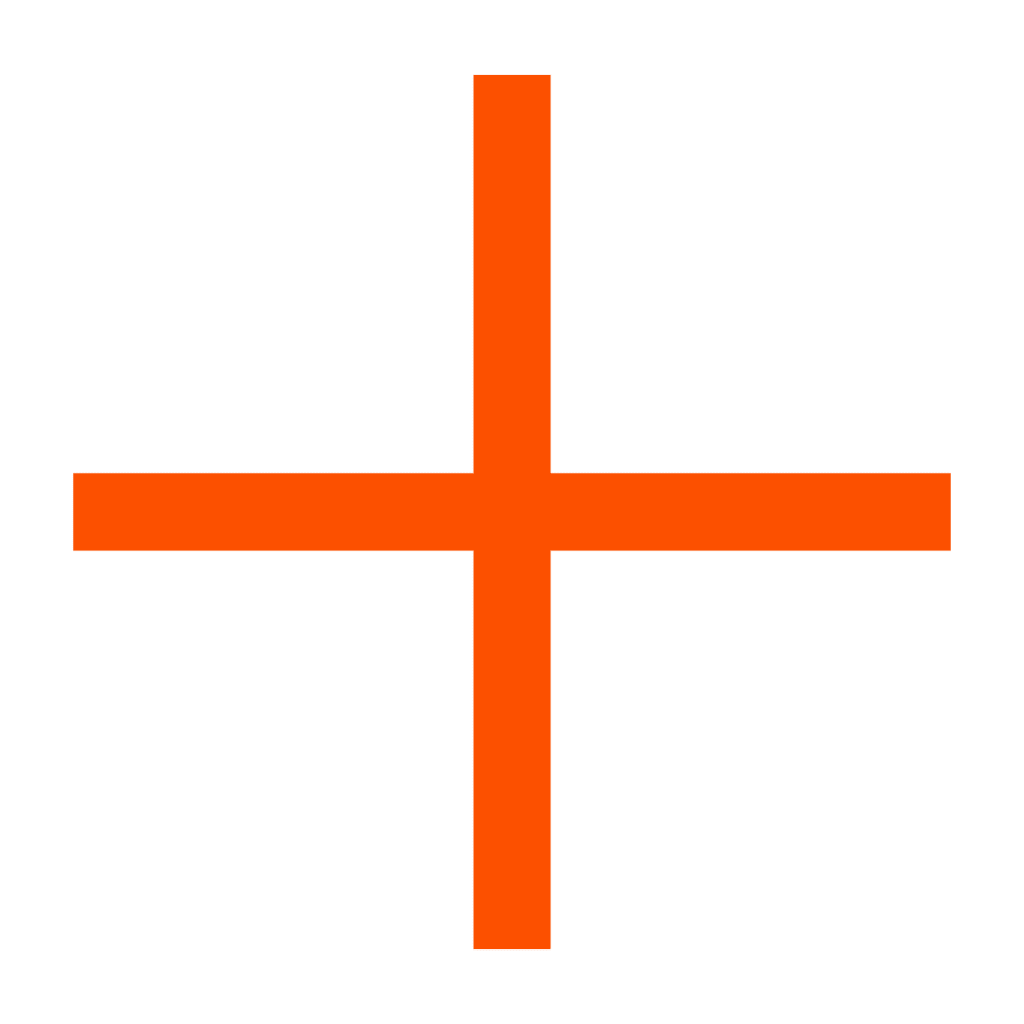
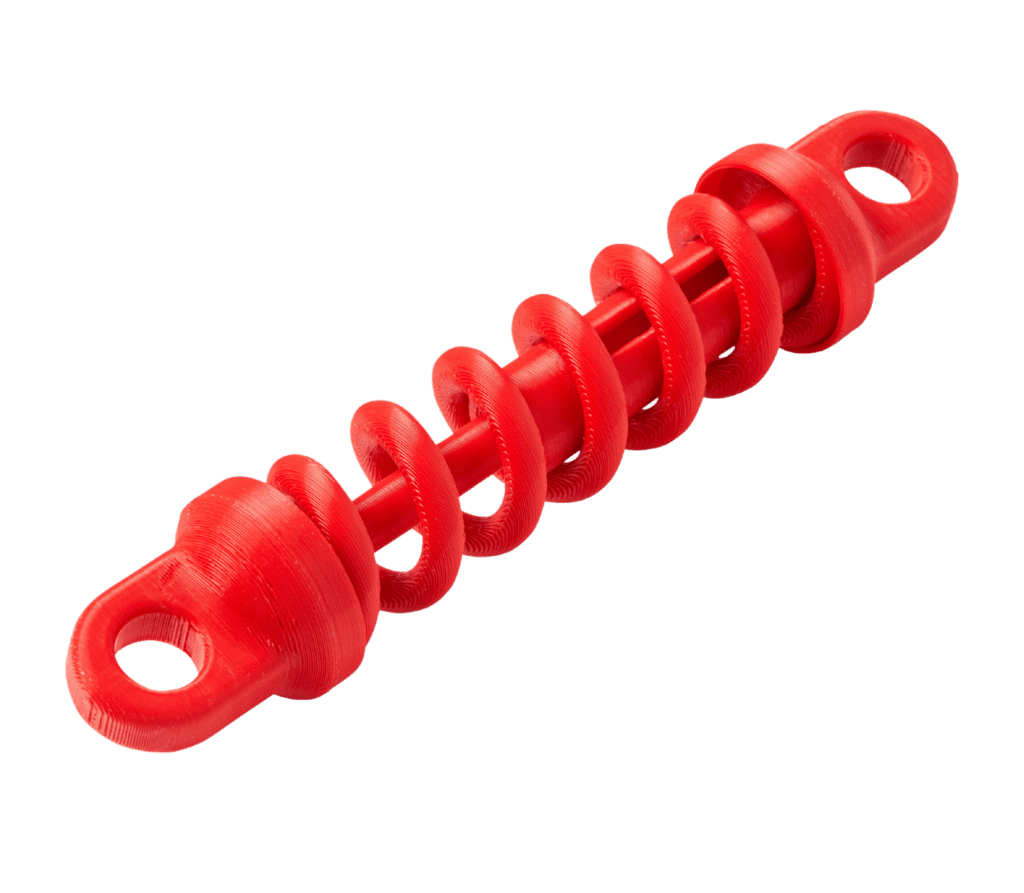
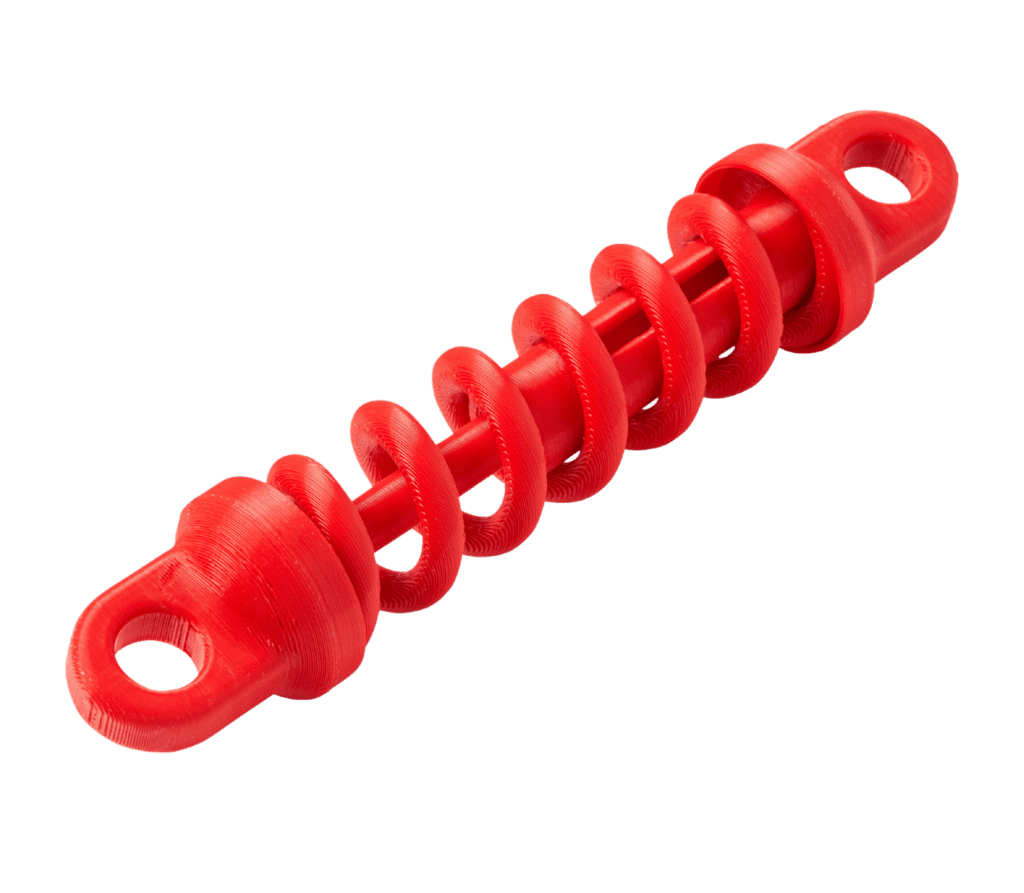
Service
We understand that not every business is ready to take the plunge into buying a new 3D printer. Our FDM service gives you peace of mind that your products and parts are made right every time. We are also on hand to support your existing process with materials not available to you, or for any necessary overspill work.
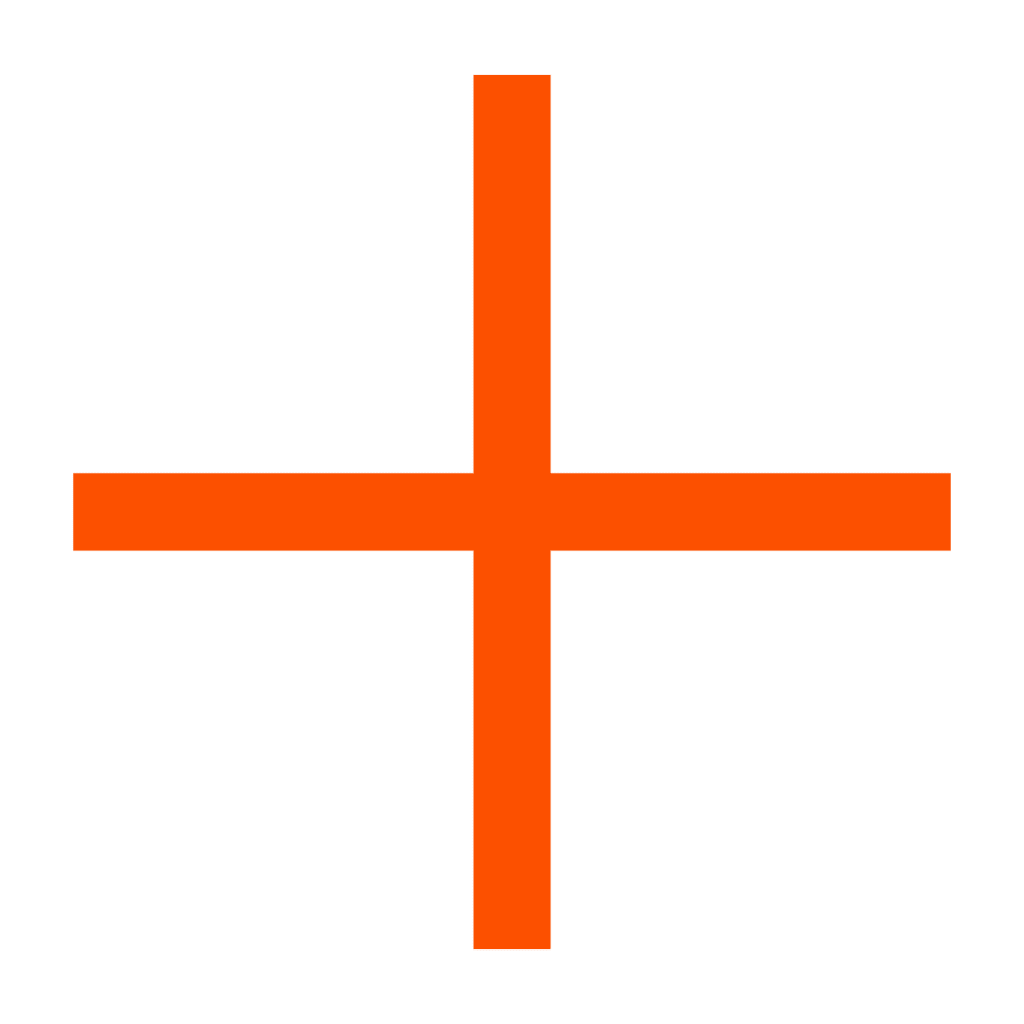
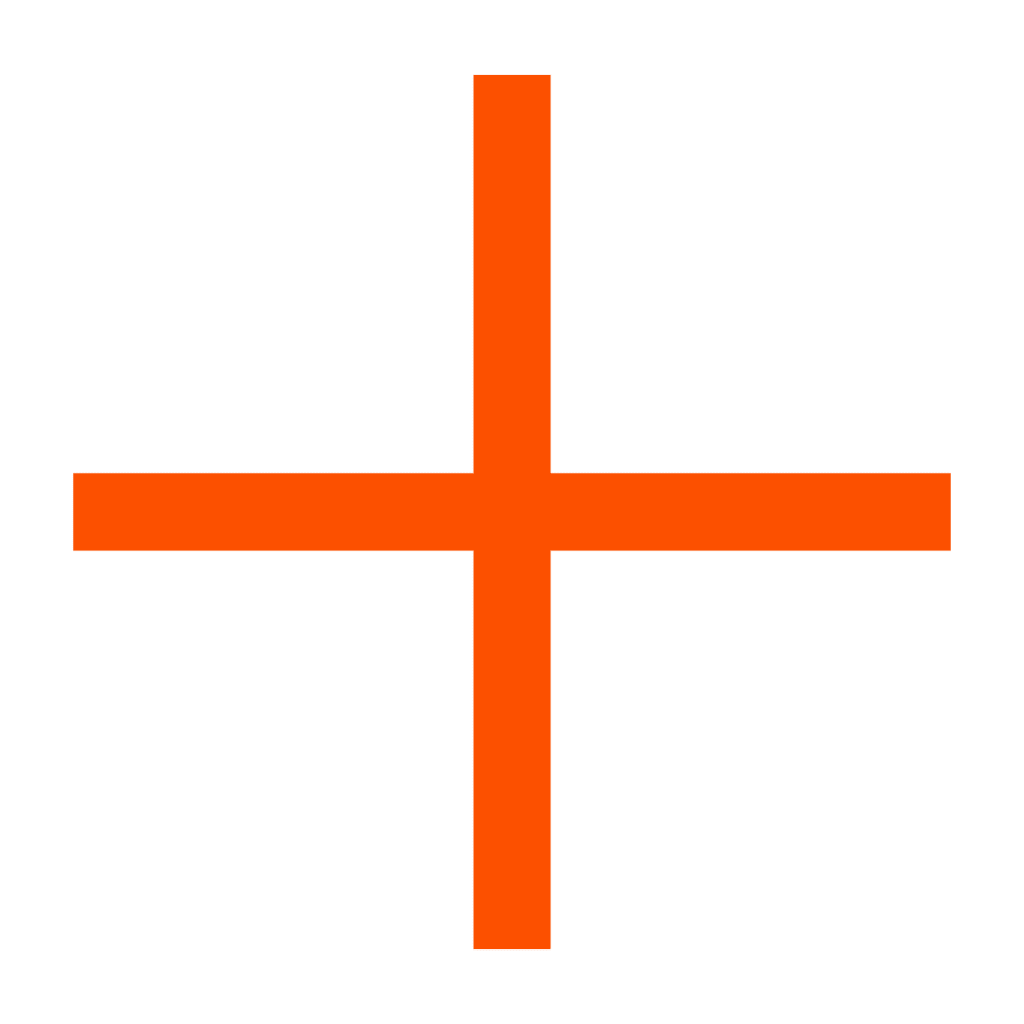
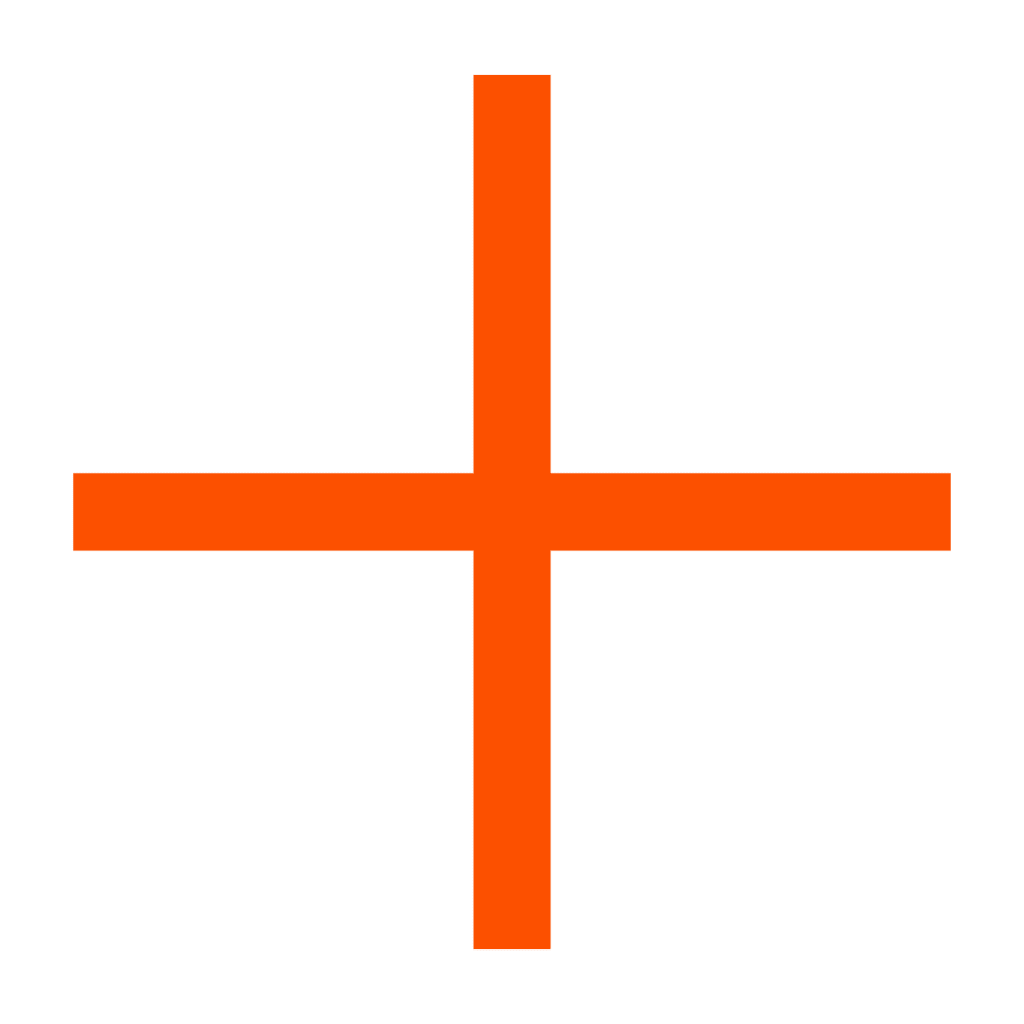
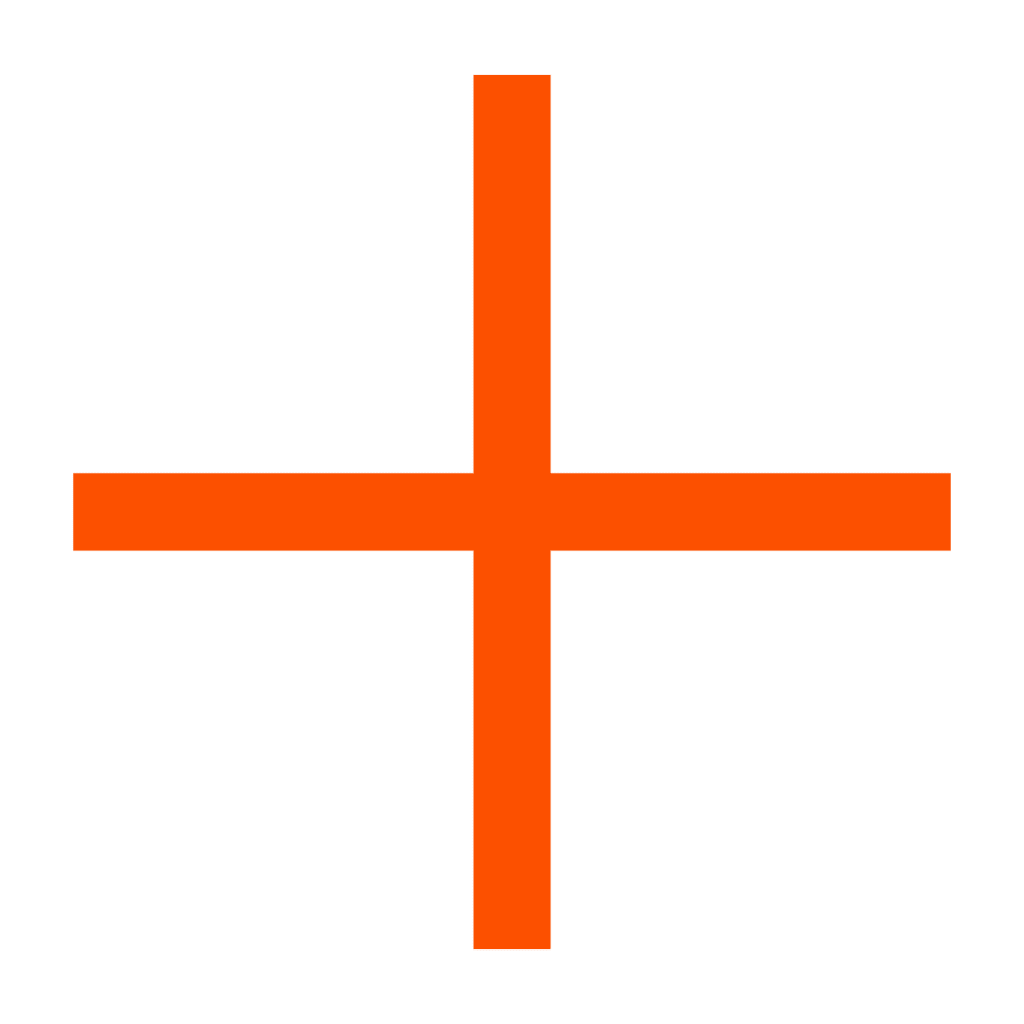
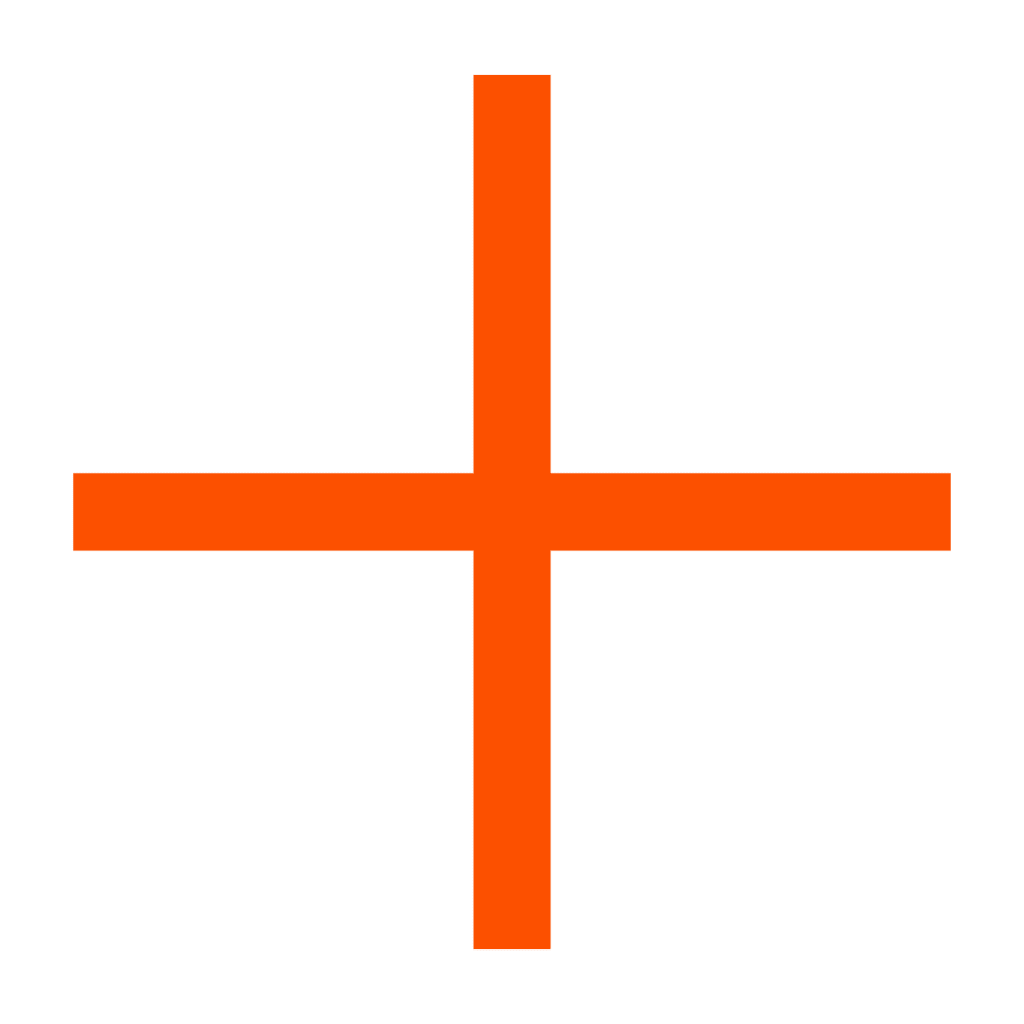
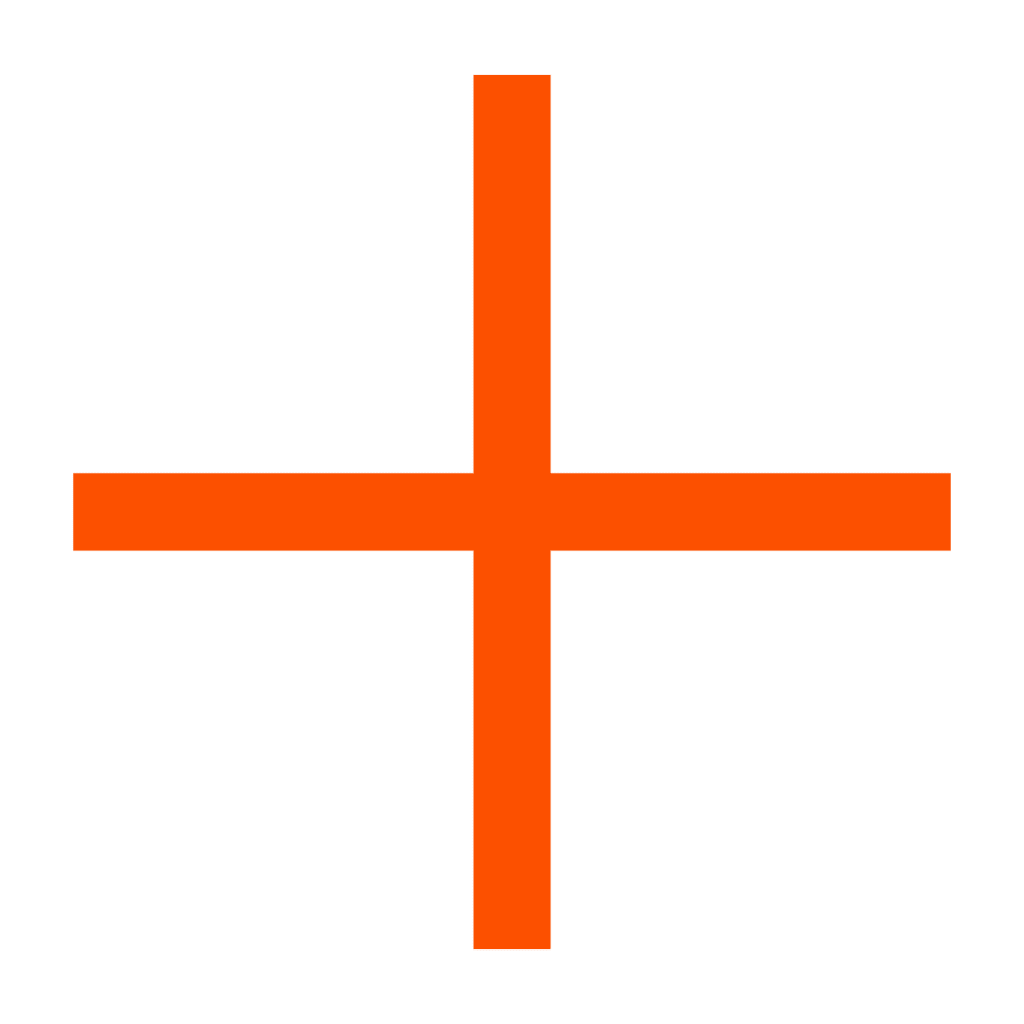


Buy
We help you get it absolutely right for your business, calculating ROIs, supporting training and maintenance and giving you the tools to unlock the full power of additive manufacturing. With SYS Systems you get the best price, the best value and the best service to help your business resolve its biggest manufacturing challenges.
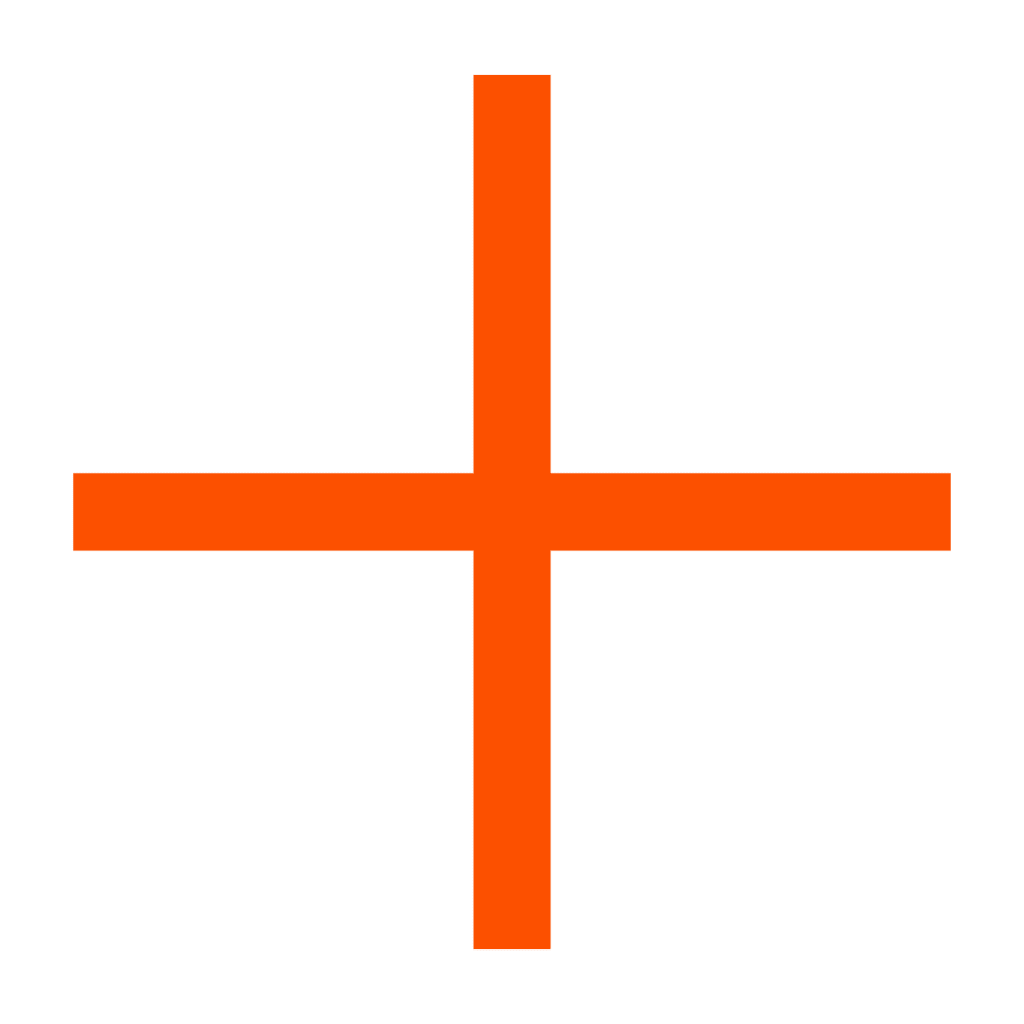
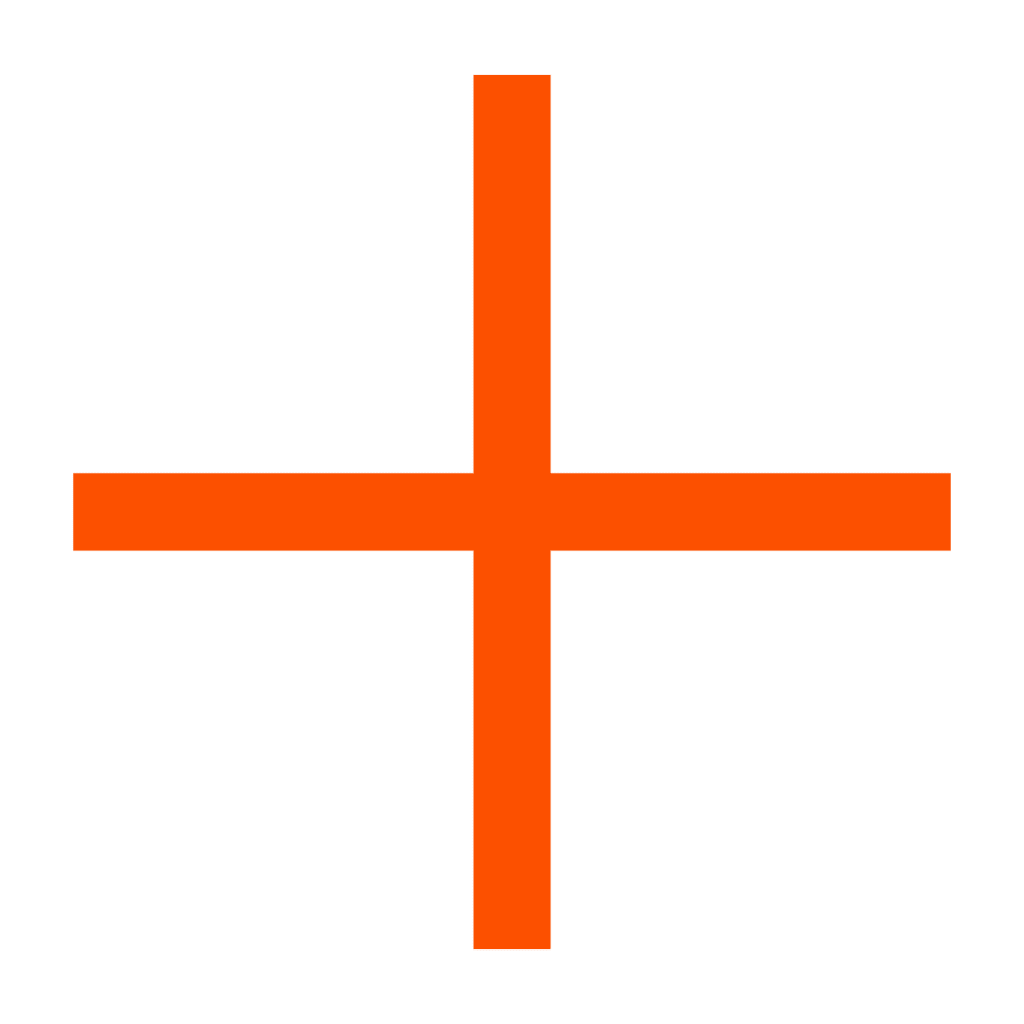
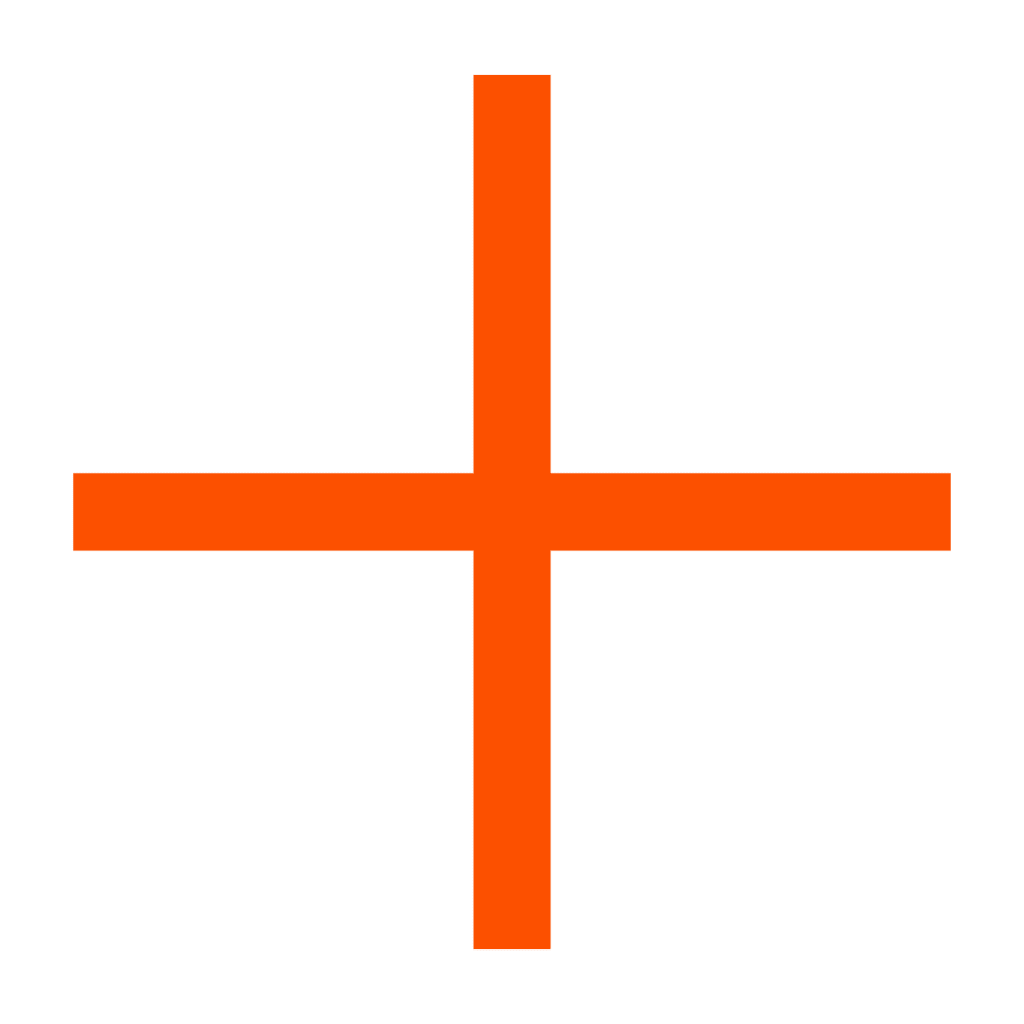
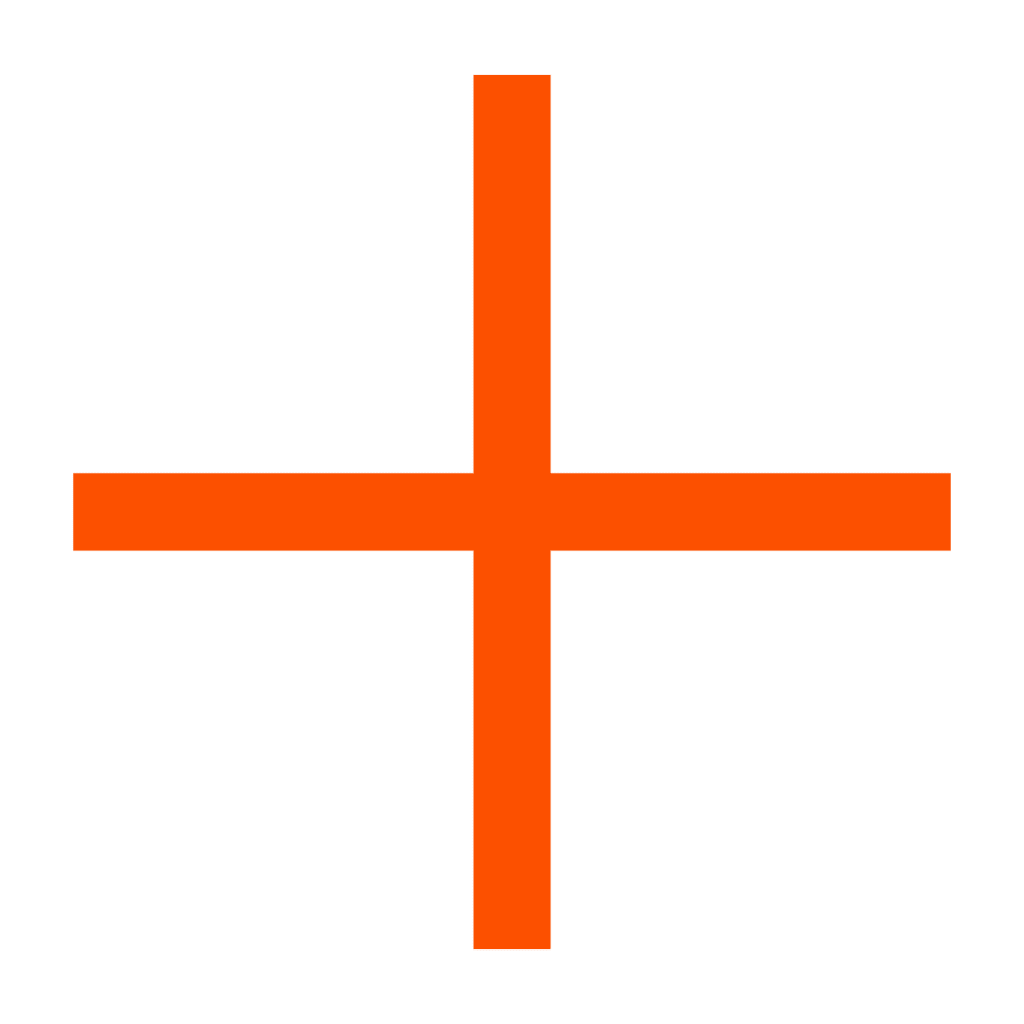
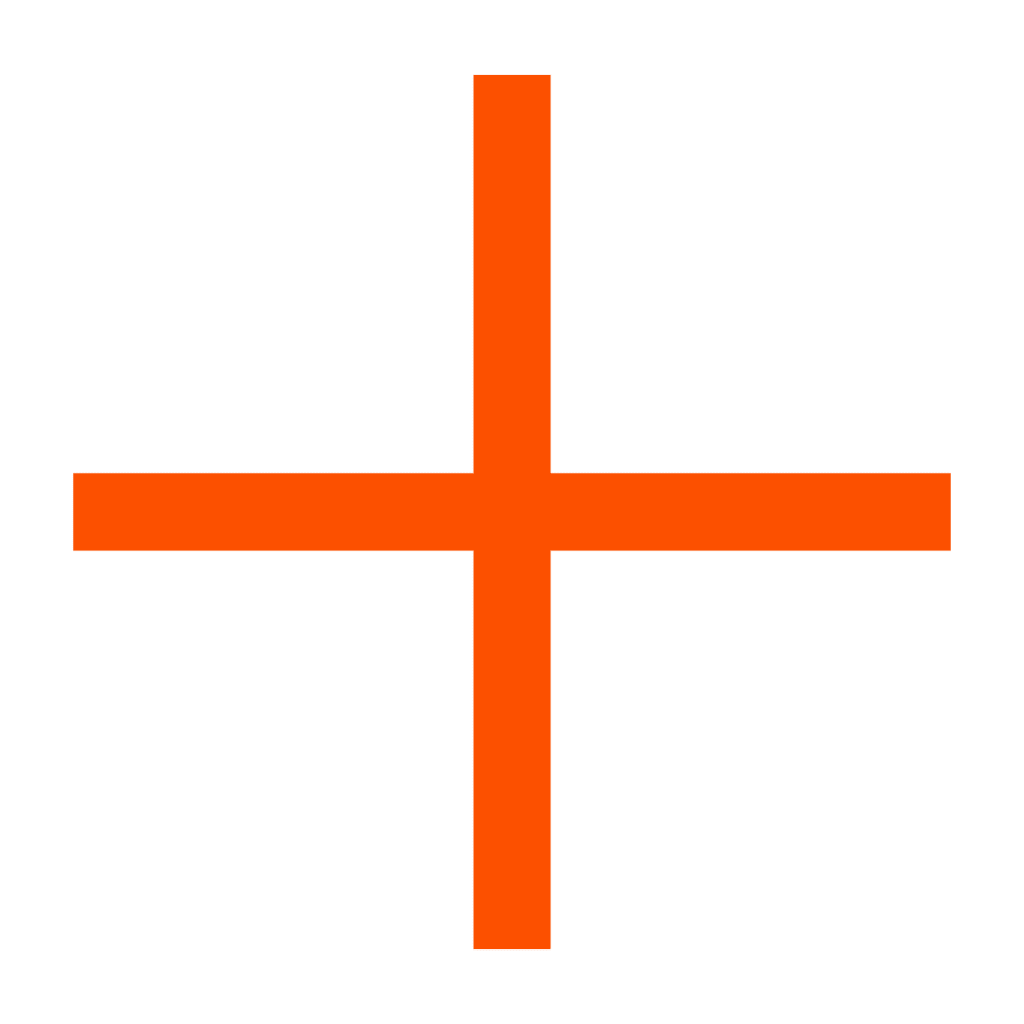
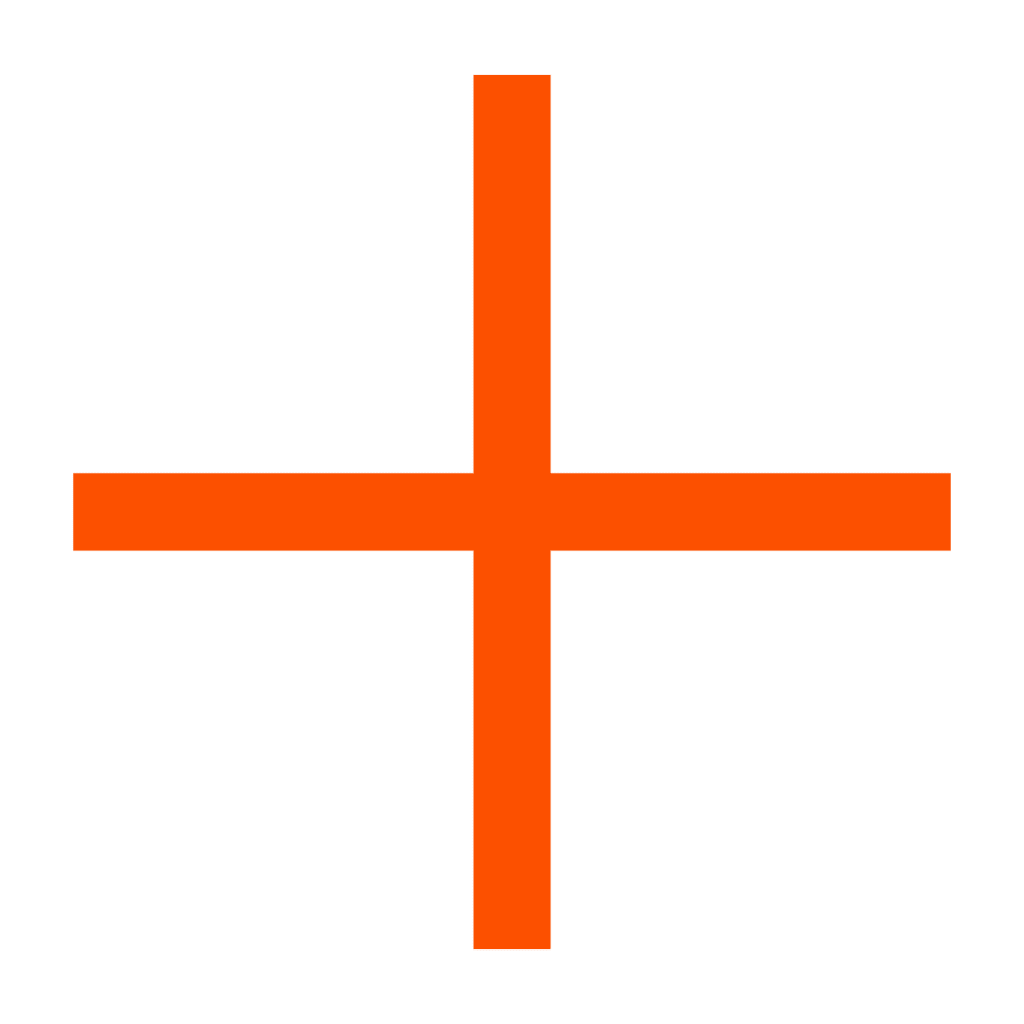