Stratasys is synonymous with 3D printing. From longstanding FDM printers to new P3 technology, a wide range of additive manufacturing materials can meet all kinds of demands.
Additive manufacturing is always improving and expanding. New printing technologies are created and new approaches to existing technologies come to light as developers find faster and more secure ways of building the products and parts required.
The various approaches that make up the whole of 3D printing technology sometimes only differ in small ways, but each one comes with its own advantages.
FDM
Fused Deposition Modelling (FDM) was developed by Stratasys co-founder Scott Crump in 1988. Using spools of filament and heated extruder heads, thermoplastics are melted and deposited, layer by layer, to build three-dimensional parts.
FDM’s main advantage lies in its ability to work with very high-performance materials. Stratasys offers Nylon 12 Carbon Fibre filament, which has already proven itself a go-to for manufacturers who require a strong and lightweight alternative to cumbersome metal tooling. 35% carbon fibre content ensures high tensile strength that can meet a wide variety of industry applications.
Other materials usable with FDM printing include food and biocompatibility-certified ULTEM resins, which possess high heat and chemical resistance, and PEKK-based Antero plastics which hold excellent mechanical properties that make them equally suitable for the factory floor and high-grade aerospace applications.
Whilst not the leading technology for aesthetic jobs that require novel textures and colours – FDM is a reliable printing process that creates tough parts when handling complex geometries. From prototyping to end-use parts, FDM can handle it all.
PolyJet
PolyJet is a material jetting process. It works using liquid photopolymers rather than thermoplastic filament. Additionally, it sprays droplets of the plastics as opposed to heating and extruding them, not dissimilar to an inkjet printer.
As they’re deposited, the droplets are cured using UV light to instantly solidify and harden them. The end results have great surface finish and smoothness. Stratasys’ version of this 3D printing technology, PolyJet, can create simulated textural finishes that look and feel like fabric, wood, and other materials.
PolyJet excels at creating prototypes, functional concepts, and models in full colour and detail. Parts built using this method have excellent surface finishing. 640,000 colour combinations using VeroVivid means that PolyJet printers close the gap between the design and reality. Shore values can be varied and even surface texture can be simulated for high-quality testing that closely mimics the end result. PolyJet 3D printing technologies have brought prototyping and design in house for many companies, simplifying processes and reducing costs and lead times.
Though it can create usable jigs and fixtures, PolyJet is best when focused on aesthetics. The textures and colours of its photopolymers make it best for fast prototyping with realistic finishes. PolyJet is the technology of choice for designers and product testers.
SAF
SAF is a Stratasys technology that employs an infrared-sensitive High Absorbing Fluid alongside the powder. This fluid is jetted into specific areas according to the shape of the layer, which is then exposed to infrared energy causing the powder to fuse. SAF creates end-use parts with production throughput.
SAF is one of several 3D printing technologies that utilise polymer powders. Differing from regular laser sintering, SAF utilises a High Absorbing Fluid (HAF) that is highly sensitive to infrared in order to fuse particles together.
Once the print bed has been coated with powder, the HAF is jetted into selective areas and exposed to IR energy. This heats and melts the powder in that area, fusing it whilst leaving the surrounding powder unchanged.
The powder is distributed in even layers with a build platform that lowers as each cross section of the part is created. Loose unprocessed powder is left to accumulate and provide support to the part, eliminating the need for separate support material. The powder bed forms a supportive ‘cake’ that parts can be nested within. Stratasys Big Wave™ powder management technology ensures that unfused powder is recycled and redistributed, making this method economical and optimised for reliable production. This allows many nested parts to be arranged within the powder ‘cake’ without concern for overhang or position along the Z axis.
Programmable Photopolymerisation (P3)
P3 exists amongst resin-based 3D printing technologies. Its focus is mass production of end-used parts, which it achieves using digital light projection (DLP). The Stratasys Origin One utilises this build method alongside a host of supporting technologies to ensure repeatable high-quality builds.
Origin One lowers its build platform into the printer’s resin tank to begin building. As light is projected and layers are cured, the platform is slowly raised until the part is complete. This method can yield highly accurate details less than 50 microns in size with a smooth surface finish.
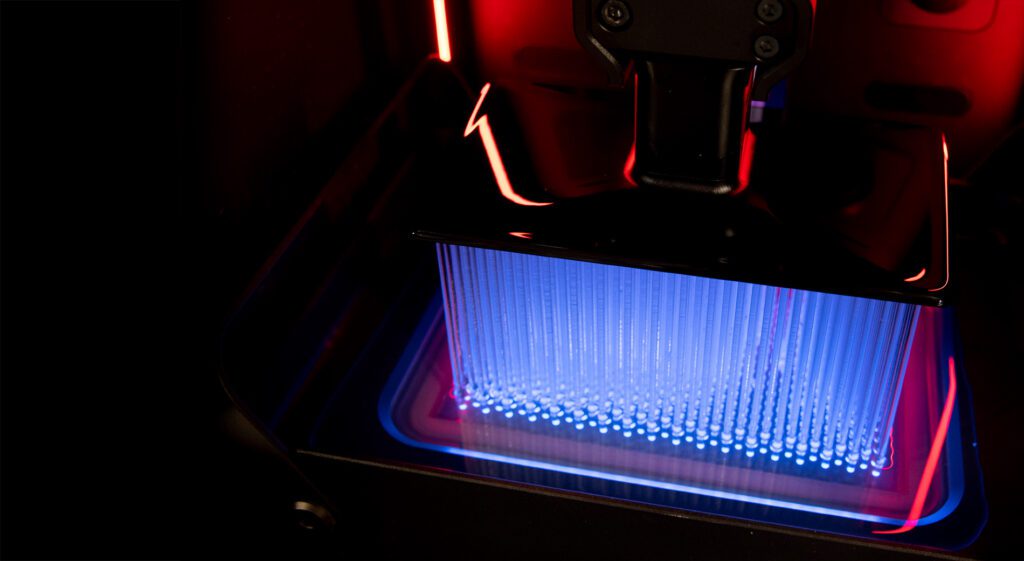
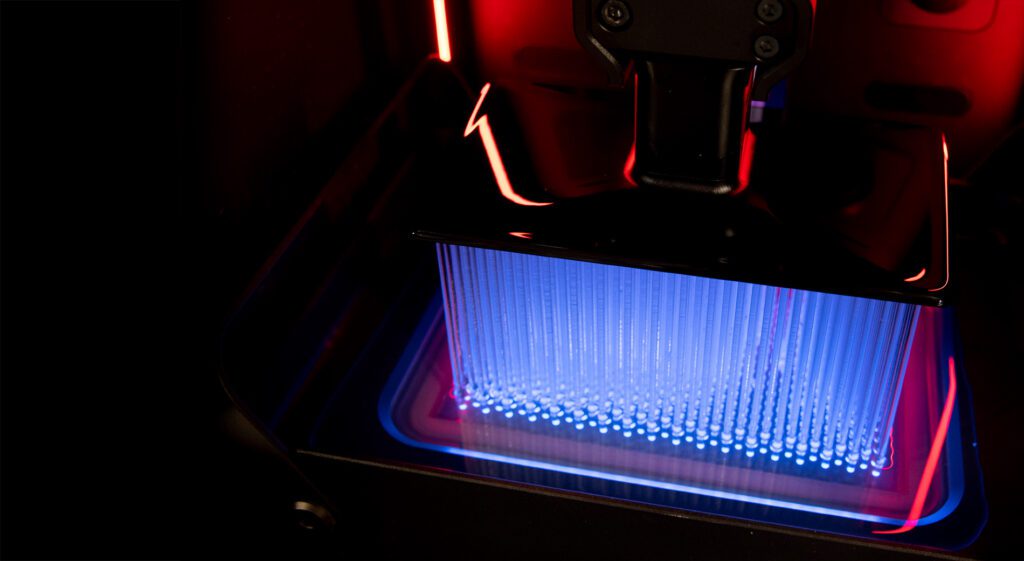
Origin One has ten industrial resins that create tough parts with properties such as superior elongation break and flexibility, biocompatibility, heat deflection at hundreds of degrees Celsius, and much more. These incredible parts can replace trusted traditional methods such as injection moulding with greater versatility and speed.
3D printing technologies are varied and none present a one-size-fits-all solution. However, with Stratasys, a machine can be found for any application.
SLA
SLA was arguably the very first 3D printing technology to be studied and built upon as a method of manufacturing. Using mirrors that direct a laser beam to the correct coordinates, the cured layer of resin is separated from the bottom of the tank and the build platform is raised up to create room for the next.
The Takeaway
Each 3D printing technology has its strengths and weaknesses, and applications in which it’s better suited than others. Some, like FDM, are adept at handling many areas across low and high-impact uses.
To better understand what one printer can do over another, we always recommend speaking to our dedicated experts at SYS Systems, certified Stratasys Platinum Partner.
Get in touch with us here and discuss additive manufacturing today.