3D printing is the process of creating objects from three-dimensional CAD files.
Most 3D printers use a plastic or composite filament, or in some cases, a powder to build a part up layer by layer to create the finished article. The 3D printing process has also been used with materials including ceramics, metals, cement and even soil.
Ultimately, 3D printing in its simplest form is the distribution of a fine thin layer of liquid or powder material onto a tray, and repeating the process until completion. The material is fused together using UV light or heat. In some processes, each layer is cured one by one, in others it is ‘fused’ collectively combining all the plastic filament or powder particles.
Manufacturers can create higher performance parts than ever before, merging the material properties that they need. Ideal for industries such as aerospace, automotive and medical where the scope and the importance of high accuracy, strength and quality is ever persistent.
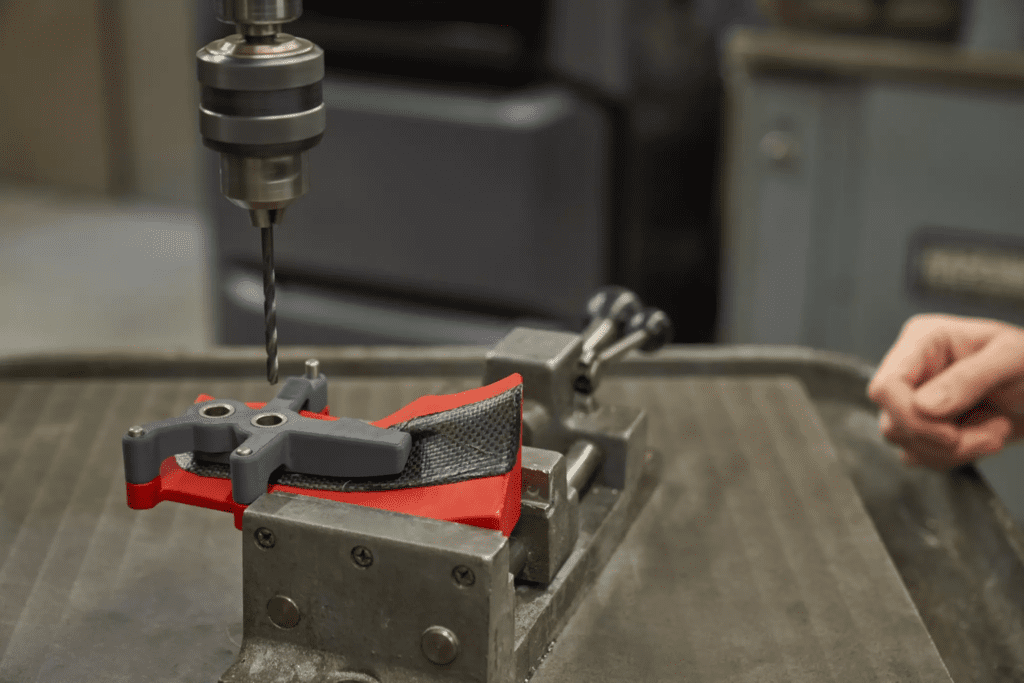
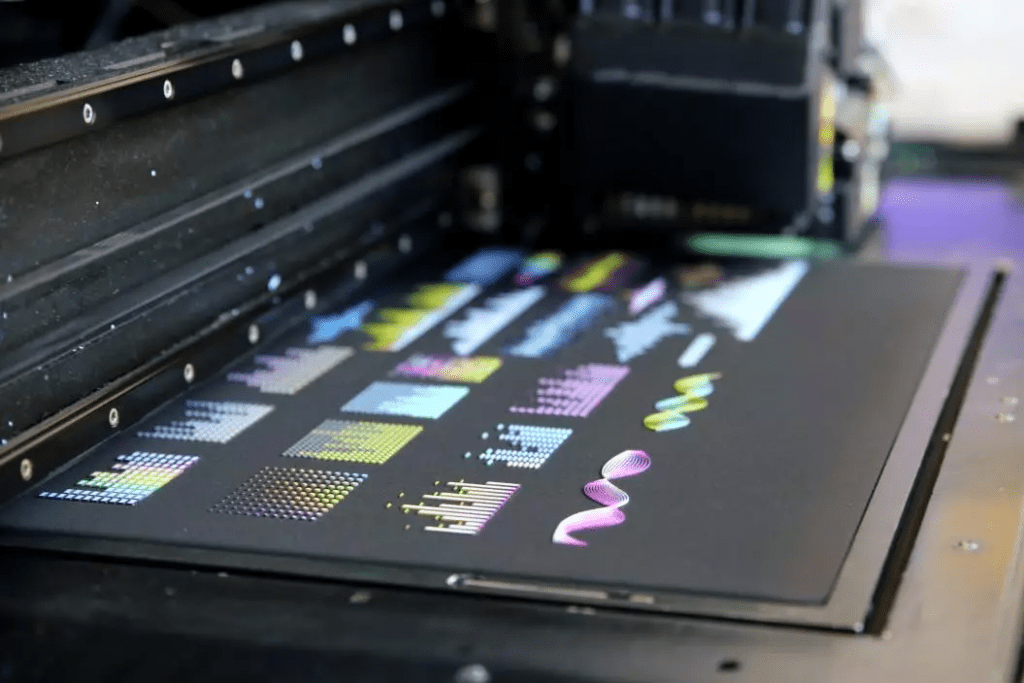
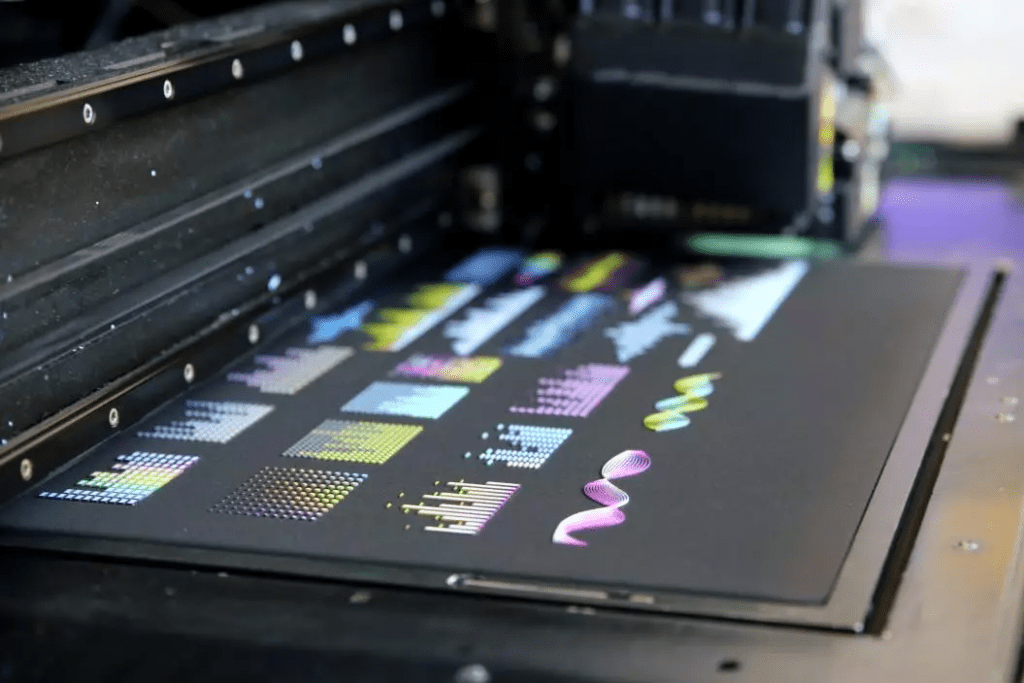
Additive not subtractive manufacturing
3D printing is also known as additive manufacturing, and is the process of adding material to a product to create it, as opposed to subtractive manufacturing where a part is created by taking material away from raw material, e.g., a sheet of metal.
The term Additive Manufacturing (AM) is often favoured by industry experts, as it refers more technically to the process of 3D printing. 3D printing also has a massive, and ever expanding hobbyist market which has largely been the reason for the use of the term Additive Manufacturing by experts.
How does 3D printing work?
Each layer is a thin slice of the object that is created using data from a computer model. The data is transferred directly from CAD files to the 3D printer, where the specifications are downloaded and used by the printer and the print head, to then distribute the filament or powder required to build the product or part. When each slice is created, it is then sprayed with a binder, which sets it in place or cured with UV light or heat before the next one is created. The object is then built up layer by layer until the part is finished and ready for post-production finishing.
The technology is similar to other forms of printing such as offset lithography, screen printing, or inkjet printing. The main difference between 3D printing and traditional printing is the addition of material layers. Therefore, objects are produced bottom-up instead of top-down. Rather than applying the forces of gravity combined with an ink, an offset or mould, a 3D print is built like a house using support materials to help maintain its structural integrity and avoid material bulges or offsets.
This process allows 3D printing to produce complex shapes that would not be possible with conventional manufacturing methods. It is also a much more cost-effective alternative to machining as it allows objects to be made using less material and labour compared to traditional methods.
What are the different 3D printing technologies?
What is SLA printing?
Stereolithography or SLA works by projecting light through a photosensitive resin to cure each layer of the object one on top of the other. The resolution is usually higher than other methods of 3D printing. It is used mainly for prototyping and small batches of functional parts. Discover more on SLA printing
What is SAF printing?
SAF or Selective Absorption Fusion technology uses powder to create end-use parts, and is by far the most scalable 3D printing technique, allowing manufacturers to produce in medium to high volume. SAF uses infrared HAF (High Absorbing Fluid) to fuse the particles of polymer powder and build parts layer by layer. Discover more on SAF printing
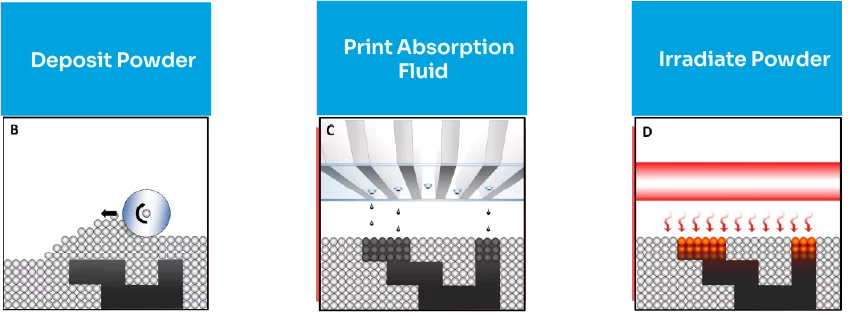
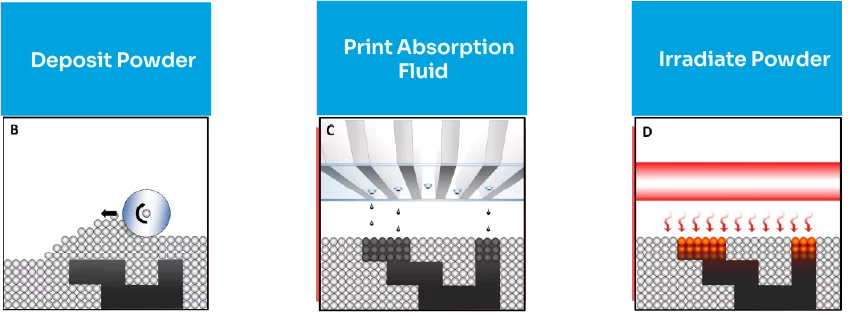
What is FDM printing?
Fused Deposition Modelling – FDM uses a heated nozzle to deposit plastic onto a platform and build an object layer by layer. This method is most commonly used for rapid prototyping of small plastic parts and products. It is the most economical method for 3D printing as it is relatively inexpensive and has a fast turnaround time. Discover more on FDM printing
What is DLP and P3 printing?
DLP or Digital Light Processing is a process whereby photopolymer parts are produced rapidly due to a UV light source curing each layer in one. The process has been developed by Stratasys in recent years, and the resulting P3 technology or Programmable Photopolymerisation combines performance and accuracy to put manufacturers in complete control of their part quality. Discover more on P3 printing
What is Polyjet printing?
Polyjet printing is as close as it gets to inkjet printing. A polyjet printer will distribute layers of liquid photopolymers onto a stage in exquisite detail. Utilising the most extensive range of colour combinations of all 3D printing techniques, as well as a wide variety of materials, Polyjet is the 3D printing process of choice for designers. Discover more on Polyjet printing
What materials are used in 3D printing?
What is a build material?
Build material refers to the main material, or materials used to create the part. Some printers are able to accommodate multiple materials, with some Stratasys printers able to print in up to 8 material channels in one print. It depends of course on the process, as the FDM and Polyjet processes have a large array of available materials, material compositions, combinations and colours. The material capabilities might be lesser with other 3D printing processes which are designed to offer different benefits, but all processes offer a range of material properties, from high rigidity to high resistance, high tensile strength to transparency.
What is support material?
Support material is a material that is used to help build the part up layer by layer. The role of the support material is to build alongside the layers of the part to ensure the structural integrity, and that the part matches the specifications and description of the CAD file. This support material is often soluble or straight-forward to remove from the part with water or soapy water.
The other method of removing the support material is known as breakaway. It depends on the print process and the printer as to which method you will use, but breakaway may require additional tooling as part of the breakaway process, often a knife or chisel before the excess resin can be washed away.
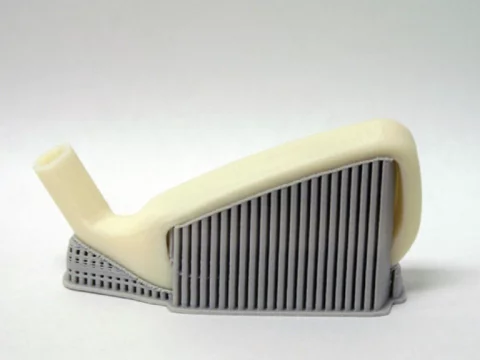
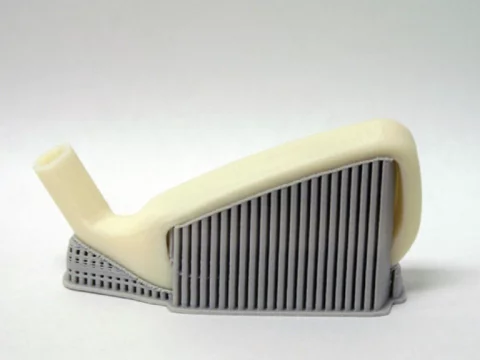
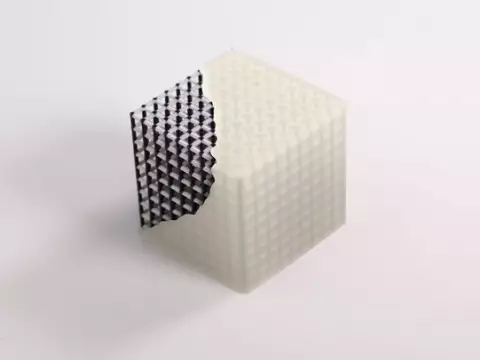
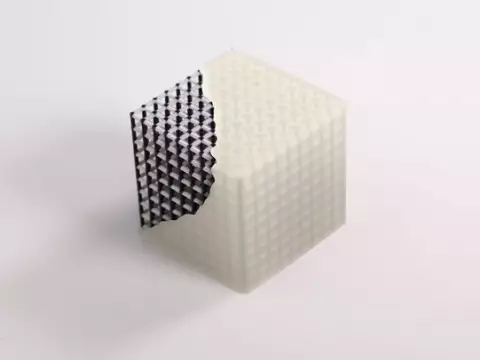
A brief history of 3D printing from prototyping to tooling and manufacturing
Initially, in its infancy 3D printing was used almost solely in industry for rapid prototyping which is what the whole industry was known as for two decades, along with the term, direct manufacturing. Since then, industries including manufacturing, aerospace and medical have used 3D printing on an ever-increasing basis, recognising its potential to create customisable parts and products, on demand, and fast. Ideal for smaller volumes, but also medium to high volume, as use-cases increase, manufacturing facilities are stocking up on 3D printers due to the flexibility it offers, reducing reliance on overseas manufacturing in volatile economic environments.
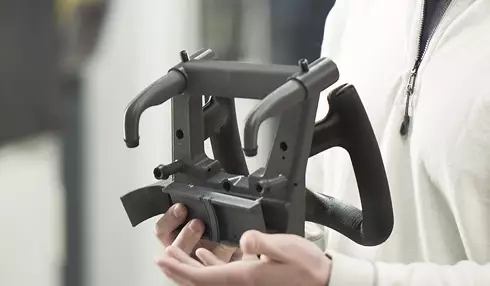
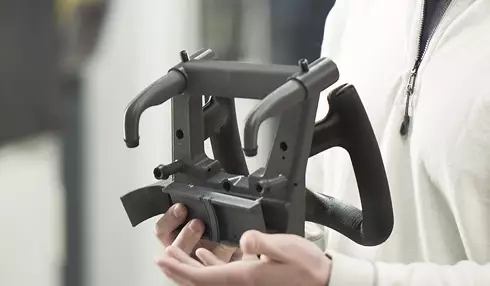
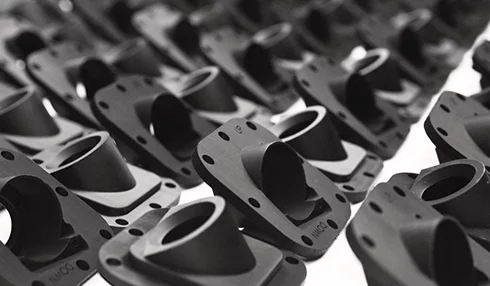
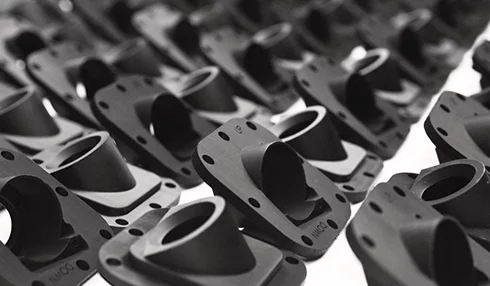
Tailor-made for specific requirements
One of the factors that has resulted in the widespread adoption of 3D printing in industry is the versatility that it offers to create without limitations. Able to create bespoke parts, products and prototypes, the creator can control variables. Owing to a wide range of available materials, particularly in plastics and composites, there is huge scope to prioritise variables in composition. This means that strength, temperature, corrosion, heat and UV resistance requirements can be accounted for, and controlled.
Manufacturers can create higher performance parts than ever before, merging the material properties that they need. Ideal for industries such as aerospace, automotive and medical where the scope and the importance of high accuracy, strength and quality is ever persistent.